Denim Manufacturing Process from Fiber to Finishing
What is denim:
Denim is a firm durable twill cotton fabric which woven with colored warp and white filling threads. Technically speaking, denim is a warp faced twill weave fabric. Here coarse and lower yarn count is used. So it is heavy fabric.
History of denim:
Denim is one of the oldest types of work cloths that is available in the fashion world. It is used for its durability and comfort. Denim comes from the French phrase “Serge de Nimes”. The 17th century “Serge de Nimes” was introduced in French. Those fabrics were produced by using a mixture of cotton and wool. Some historians believe that it was first worn by sailors of Portugal. Initially it was worn by mechanics and miners. In the 21st century denim comes in many different styles including carpenters, sportswear, khakis, chinos and combat. Now it is true that the millions of people around the world favorite choice is denim cloth.
Types of denim fabric:
There are various types of denim. Most popular types of denim are given below:
- Dry denim
- Selvedge denim
- Stretch denim
- Color denim
- Reverse denim
- Vintage denim
- Ecro denim
- Marble denim
- Crushed denim etc



1. Dry denim:
Dry denim is opposed to wash denim that means unwash after being dyed during its production.
2. Selvedge denim:
Selvage denim is a self-finished denim where the edge ensures the fabric won't unravel. It is made on a shuttle loom that means the resulting fabric is narrower. Selvedge denim has become more desirable than non-selvedge. Selvedge tends to have a tighter, denser weave than non-selvedge.
3. Stretch denim:
Stretch denim is a relatively new type of denim fabric. This type of denim is made with cotton or cotton/polyester blend that incorporates a small amount of elastane, a stretchy, synthetic fiber, also known as Spandex, or Lycra, into the fabric. Now stretch denim is popular for its relaxed fit.
4. Color denim:
Colored denim fabrics become woven. This denim is manufactured with dyed yarn either warp or weft. This kind of fabric can be obtained by piece dyeing process.
5. Reverse denim:
Reverse denim fabric is that, where the face side and reverse side are same.
6. Vintage denim:
It is old type looked denim. Vintage denim are made by heavy stone wash or a cellulose enzyme wash with bleach or without bleach.
Dry denim is opposed to wash denim that means unwash after being dyed during its production.
2. Selvedge denim:
Selvage denim is a self-finished denim where the edge ensures the fabric won't unravel. It is made on a shuttle loom that means the resulting fabric is narrower. Selvedge denim has become more desirable than non-selvedge. Selvedge tends to have a tighter, denser weave than non-selvedge.
3. Stretch denim:
Stretch denim is a relatively new type of denim fabric. This type of denim is made with cotton or cotton/polyester blend that incorporates a small amount of elastane, a stretchy, synthetic fiber, also known as Spandex, or Lycra, into the fabric. Now stretch denim is popular for its relaxed fit.
4. Color denim:
Colored denim fabrics become woven. This denim is manufactured with dyed yarn either warp or weft. This kind of fabric can be obtained by piece dyeing process.
5. Reverse denim:
Reverse denim fabric is that, where the face side and reverse side are same.
6. Vintage denim:
It is old type looked denim. Vintage denim are made by heavy stone wash or a cellulose enzyme wash with bleach or without bleach.
Denim Fabric Manufacturing Process:
Denim is 100% cotton woven fabric. So, it is strong and durable. Generally blue denim is warp faced cotton fabric with 3x1 twill construction where warp is dyed solid color and weft is undyed.
![]() |
Fig: Denim fabric manufacturing |
Lower count and coarse yarn is used for denim making. Fiber quality is not good. Denim yarn produced from open end spinning system. Probably the most important characteristics of the sliver is its cleanliness with particular care to be given to dust remove.
In ring spun yarn, a high incident of nep in the yarn will cause uneven dye uptake during the warp yarn preparation. It is observed that modern blow room line create neps. Up to an increase of 100% over neps in raw cotton that will still allow the carding machine to be able to remove most of these objectionable faults.
Coarse count yarn in denim refers to less than 8s Ne and fine count is 9s to 16s. Mixing requirements for rope dyed warp open end yarns are higher.
Dyeing and sizing process of denim yarn:
In denim fabric, warp yarns are indigo dyed. There are various types of dyeing and sizing process which can be classified into four types. Such as-
- Continuous indigo rope dyeing and sizing
- Continuous indigo dyeing and sizing
- Indigo back beam dyeing and sizing
The yarn which we get from ring frame is wound into cheeses or cones and then placed on the ball warper on which 350-400 threads are formed into a rope. During this process, 12-24 ropes are dyed at a time based on the size of the rope dyeing plant.
2. Continuous indigo dyeing and sizing:
During this process, back beams are processed on the dyeing and sizing machine instead of ropes. The warp are dyed, oxidized, dried and sized at a once.
3. Indigo back beam dyeing and sizing:
According to this process dyeing and sizing is done in two stages. In the 1st stage, back beams are dyed, oxidized, dried and wound on a batch roll. The batch roll is then sized, dried and wound on a weaver’s beam.
Weaving process of denim fabric:
Weaving is done by interlacement of warp and weft threads, where warp yarns are indigo dyed. In this system warp thread is in the form of sheet. And weft thread is inserted between two layers of warp sheet by means of a suitable carrier such as shuttle, projectile, rapier, air jet, water jet etc.
Finishing process of denim fabrics:
Final woven fabrics, which is wound on a cloth roll that we get from weaving machine at particular intervals and checked on inspection machine. So that any possible weaving fault can be detected. Then its goes through various finishing process. Such as brushing, singeing, washing, impregnation for dressing and drying. Brushing and singeing remove impurities and hairiness of the denim fabric. After complete all finishing process then it is sent to for garment manufacturing.
Denim fabric dyeing: Dyeing [rocess of denim fabric are two types. These are indigo dyeing and sulphur Dyeing. Indigo produce conventional blue color and shade alike to blue color. Sulphur dyeing is used to denim produce particular colors like black, cherry, grey, rust mustard and lime. Both are vat dyestuff. Both are insoluble in water and have a very poor affinity to cellulose fibers like cotton.
Denim washing process:
The wash out effect is achieved by removing dyestuff from fabric to get popular abraded, worn out look during washing process.
Wash can be divided into two types. Such as-
- Mechanical wash
- Chemical wash
Mechanical wash contains garment wash, stone wash, sandblasting etc.
2. Chemical wash:
Chemical wash contains acid wash, enzyme wash, bleaching wash etc.
Popular washing of denim fabric:
Garment washing:
Garment wash is one type of short time wash. It is done for soft hand feel and natural cleanness. This type of wash is done by only water. Many time use detergent and many types of softeners. Finally the fabric is softened and lubricated.
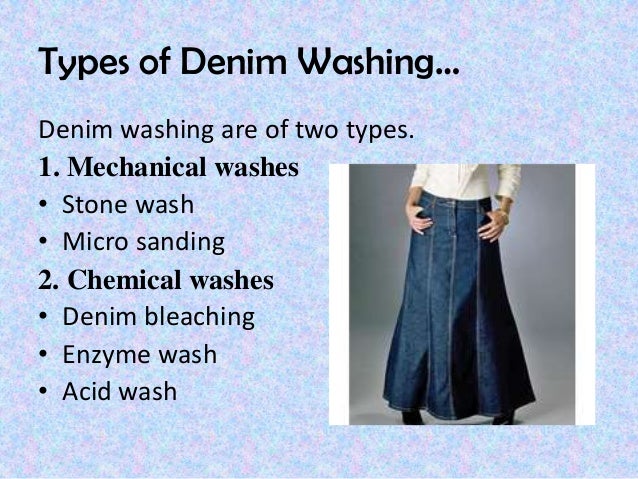
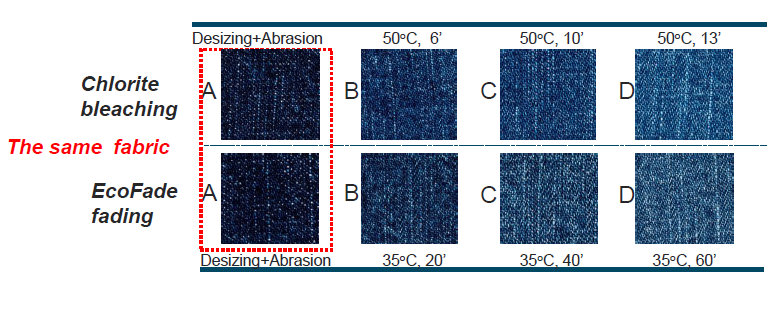
Stone Wash
Stone
create a fading look in denim and increase softness and flexibility.
This method has been improved by using other materials during wash. In
this washing process the newly dyed jeans are put in washing machine and
tumbled by pumice stones as abrasion. Stones have rough surface and
remove some of the dyes particle from the surface of the fabric to give
worn-out effect.
Acid Wash is one of the fashionable wash method. It can give the garments marble effect on the fabric surface and shaded look. In this process, pumice stone or rubber ball used with bleaching agent such as sodium hypochlorite or KMnO4. Then neutral the garments and dried.
Enzyme wash:
In washing, enzyme wash is relatively new technology for denim to achieve the worn appearance and to provide soft hand feel. Enzyme remove indigo dye and hairiness of cellulose fibers from the fabric surface.
Bleaching wash:
The bleaching effect is done by using an oxidative bleaching agent eg. Sodium hypochlorite, calcium hypochlorite or potassium permanganate with or without stone addition. The dark blue shade is decolorized by the bleaching chemical which destroy the indigo dye molecules. .
Finishing process of denim garments:
Denim finishing will give your garments the final touch to create the right high quality fashion style. Getting the unique look with a superior reduction of back. Staining is fast and easy, wet and dry technique such as whiskering, brushing, crushing, washing, etc are all these technique give the fabric softer feel. Enhance its appeal without any strength loss and improve wear life. Resin finish is done for 3D effect.
Brushing/grinding:
Brushing/grinding (manual or mechanical) is used manually or mechanically for the worn-out effect, abraded look or used look. Some mechanical processes have been developed that are based on mechanical abrasion by which the indigo can be removed. Some of these processes are sueding, raising, immersing, peaching and brushing.
Advantages of these processes are as follows:
- Control of the abrasion.
- Different looks on the garment can be achieved.
- All are dry processes.
- Economical, ecological and environmentally friendly.
![]() |
Figure-2: Marking the location for brushing |
![]() |
Figure-3: Hand brushing of denim |
![]() |
Figure-4: Mechanical brushing of denim |
![]() |
Figure-5: Grinding mark on a pocket edge of jeans |
![]() |
Figure-6: Grinding mark in a bottom hem of jeans |
To give a worn effect or abraded or used look, some mechanical processes were developed. These are based on mechanical abrasion, which removes the indigo. Some of these processes are sueding, raising, immersing, peaching and brushing.
Advantages of these processes are:
Abrasion can be controlled.
- A different look to the garment can be achieved.
- All are dry processes.
- The processes are economically, ecologically and environmentally friendly.
Wishkering refers to thin fading lines formed from creases that are usually found on the front pocket area of jeans. It is one of the most important design of a used look denim garment. Now a days it is a common drying process for denim wash.
Ozone fading:
Ozone destroys indigo color on denim in a manner similar to bleaching.O Zone Fading of washed and bleached denim is primarily caused by the oxidative effect of ozone on the indigo dye, the contaminants and the applied additives. Ozone fading gives the advantage of fading with a minimum or hardly any loss.
Laser treatment:
Laser Fading or marking is a popular dry process for denim now a day. A carbon dioxide (CO2) laser was used for the colour-fading treatment of denim fabrics. It is sustainable, environment friendly and emerging industrial approaches for the finishing treatments of the denim jeans.
Waterjet fading:
Hydrojet treatment has been developed for patterning and/or enhancing the surface finish, texture, durability and other characteristics of denim garments. Hydrojet treatment generally involves exposing one or both surfaces of the garment through hydrojet nozzles. The degree of colour washout, clarity of patterns and softness of the resulting fabric are related to the type of dye in the fabric and the amount and manner of fluid impact energy applied to the fabric. Particularly good results are obtained with blue indigo dyed denim. As this process does not involve any chemical, it is pollution free. A water recycling system can make this a very economical and environmentally friendly way of denim processing. Colour washout of dye in the striped areas produces a faded effect without blurring, loss of fabric strength or durability, or excessive warp shrinkage.
Dip dyeing:
In dip dyeing, dip dyeing machine is used to achieve special effects on denim garments. Direct dye is commonly used but the colour fastness is comparatively poor and therefore fixation is required to improve fastness. Pigments can also be used for dip dyeing. If a bleaching agent is used, bleaching effect can be achieved on garments.
Pigment washing:
Pigment washing is generally used on pigment dyed or printed garments by applying pigments.
Pigment washing is required for the following reasons:
- To get fading effect/old looking effect on garments and also the seam area.
- For a soft feel to wear the garment after purchasing.
- To achieve the buyer’s washing standard.
- To increase the colour and rubbing fastness.
Flow chart of pigment washing:
The basic steps of pigment washing are as follows:
Immersing garment in pigment
↓
Drying
↓
Baking (130–150 °C)
↓
Washing (with or without pumice stones/with or without enzyme, 30–90 min)
↓
Washing twice with water at 70 °C
↓
Removing stones
↓
Softening
↓
Drying.
Tinting:
After different types of process denim or jeans are dyed with very light color (.001% or .002% yellow or pink). This dyeing process is called Tinting/Overdyeing. Tinting of denim garments is usually done after the stone wash process.
Tie dyeing:
In tie dyeing, a rubber band or similar material is used to tie/bunch the denim garment to make different patterns. Then when carrying out dyeing with a direct dye, the dye cannot enter the tied portion. After dyeing, patterns can be created and fixation is needed. Pigments can also be used in tie dyeing. If bleaching agent is used, bleaching effect can be obtained, which is called ‘tie bleach’.
Plasma treatment on denim:
Plasma has been used in the treatment of textiles over the past 2 decades, but a generally available and implemented technology has yet to be developed. Nevertheless, several industrial devices are available as well as numerous examples of custom-designed plasma processing stages for specific industrial production lines. Two directions for development are atmospheric pressure devices and low-pressure plasmas.
There are numerous solutions for atmospheric pressure (or pressures of the order of several 100 Torr) devices, which include glow regime of dielectric barrier discharges and corona discharges. Low-pressure devices, in particular radio-frequency (RF)- powered plasma sources, allow easier control of properties and provide greater stability and uniformity at the cost of more complex handling of the fabric. Corona and RF low-pressure plasma treatments brought about an increase in denim lightness, indicating a removal of indigo dye from the fabric surface. The increased yellowness of the treated denim was more pronounced in case of corona and low-pressure plasma in air in comparison with low-pressure RF plasma in argon. This can be associated with the production of chemically active molecules and radicals in gas mixtures containing oxygen, which consequently leads to an oxidation of dyes.
Low-pressure plasma and corona treatments can be a viable alternative to conventional bio-stoning to obtaining the ‘worn’ look of indigo-dyed denim fabric. In addition to satisfactory colour change effects, the main advantages of these treatments are the lack of water consumption and shorter process duration. However, it requires further research to avoid an increase in yellowness and the appearance of a harsh fabric handle.
Corona and RF low-pressure plasma treatments brought about an increase in denim lightness, indicating a removal of indigo dye from the fabric’s surface. The increased yellowness of the treated denim was more pronounced in the case of corona and low-pressure plasma in air compared with low-pressure RF plasma in argon. The formation of pits and striations on the fibre’s surface was more prominent after low-pressure RF plasma than after corona treatment.
Conclusion:
Now a days denim garments is not only worn as a dress but also used for fashion purpose. Men and women both wear denim and jeans products. So improving quality day by day and increasing versatile variation in denim products.