PROCESS CONTROL IN CARDING
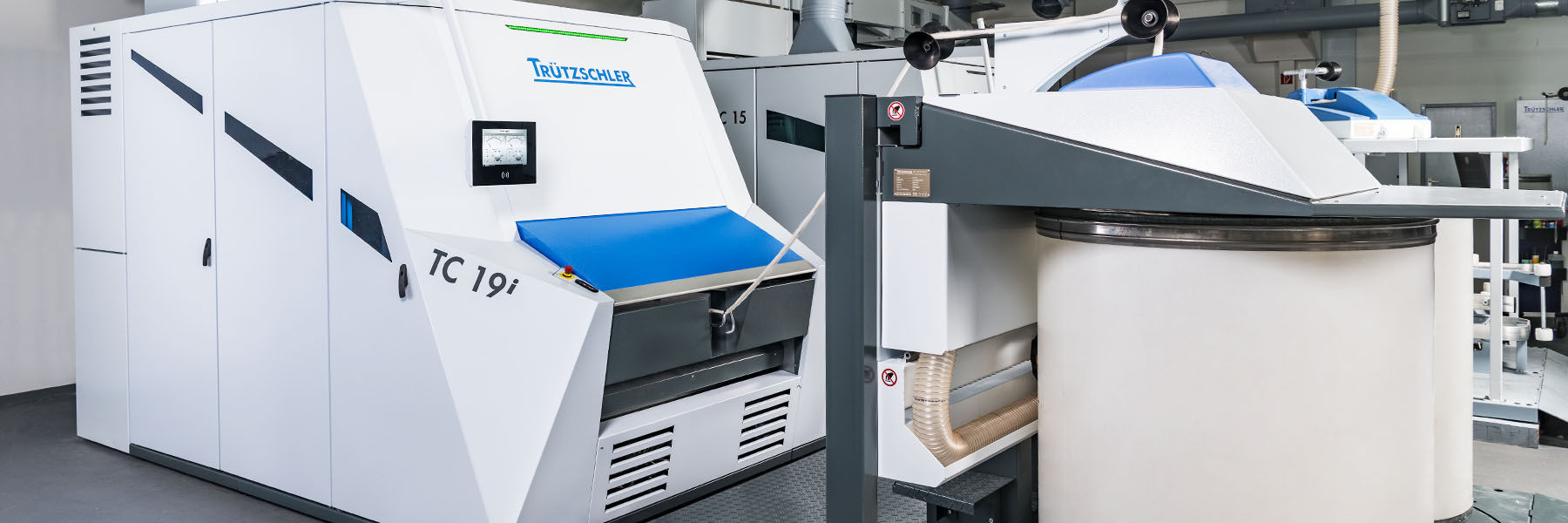
Heart of the Spinning process is Carding and it is the most important process in yarn manufacturing. It contributes a lot to the yarn quality. The following process parameters and specifications are to be selected properly to produce a good quality yarn with a lower manufacturing cost.
THEORIES OF CARDING
Classical
theory
According to this theory, a
fibre can be carded between two oppositely inclined wire points covered
surfaces moving with a high relative speed, provided the wire are so inclined
that the sliding component of tension acting in the fibre is strong enough to
move the fibre down the wire towards its base. This is fulfilled only when
cot
α>µ
Where,
α=
inclination of wire point
µ=
coefficient of friction between the fibre & wire.
The classical theory does
not take into account the centrifugal force & presence of air current due
to rotating elements and it is argued that the carding force which slides fibre
down the wire is so small in comparison to compression & centrifugal force
that it has practically no effect on the filling of the clothing.
Strangs
theory
This theory is based on
Prandtls Boundarylayer theory. In a card, cylinder may be considered to be
enclosed from all sides by flats, back & front plates, licker in, doffer
and undercasing, rotates in medium of still air. According to boundary layer
theory, a series of concentric layers of air of infinitesimal thickness
surround the cylinder. As a, these layers also rotate along with the cylinder
with different velocities. The velocity of the layer in contact with the
cylinder surface will be equal to the cylinder. The velocities of each
successive layers become less & less as its distance from the cylinder
surface increases until a layer close to the base of flat wires is reached
where the velocity is low. The presence of surrounding air current has been
confirmed by Kamogawa, Kanda & Imami, Krylov. Because air has such a
different velocities, within the space between flats & cylinder. When a
tuft is introduced in this boundary layer, it is subjected to terrific force caused
by the shearing action of air. The air shear force on a tuft can be given by
following equation.
F =
RVA/d
Where,
R=
coefficient of viscosity of air at given temperature (poise)
V=
velocity of air current (m/s)
A=
projected area of tuft in the
d=
depth of air boundary layer (m)
The depth of boundary layer
appears to be the distance between of wire on cylinder & flats. The force
therefore increases as the setting between flats & cylinder reduced. It is
this shear force that separate the fibre tufts into individual fibres. The
reason of fibre transfer from licker in to cylinder has been assigned to the
boundary layer of licker in & cylinder. The air stream around cylinder
having higher velocity removes fibre from licker in around which air stream
revolves at lower velocity. A theory explaining carding action solely by
boundary layer and shearing force of air current is unrealistic since carding
has found to occur even at very speeds. However, air current which is
definitely present due to rotating cylindrical element may have some role in
carding.
Kaufmans
Theory
Tufts held on cylindrical surface approach to cylinder flat zone at very high speed and are introduced into the narrow gap between the flats &cylinder wire points, which is generally much lesser in dimension than size of tufts. The resulting compression force, the fibres into the wire clothing of both flats & cylinder since the flats are practically stationary as compared to fast moving cylinder surface, the loading factor of compression force against the flat is greater than that against cylinder which is due its movement present larger surface area for the same compression force. According to Kaufman’s calculation, the compression force against cylinder acts on 6 time larger surface as compared to flat surface. The penetration of teeth into the tuft immediately followed by shearing action on tuft due to great difference in speed between flat & cylinder. As a result, the tuft is pulled apart into pieces. The process repeats itself when a part of tuft is held by cylinder approach the subsequent flats and this goes on. As a result, the size of tuft diminishes progressively. Generally, the opening and separation processis over by the time, the tuft goes to 5th& 6th flat location. As a result of carding action, the flat gets loaded with fibre & the cylinder is evenly covered by separated fibres. The drawing apart of fibre between the two surfaces may also be considered as the process of interaction of friction field created between the fibres and wire points of cylinder & between fibre and wire points of flat place one above the other.
The carding quality could be judged by
•Transfer Efficiency %
•NEP Removal Efficiency.
•Fiber Arrangement in Sliver
"Transfer Efficiency is defined as the percentage of fiber transferred to dofferfrom cylinder per revolution of cylinder." The Transfer Efficiency of card is important from the point of view of determining the level of loading of the cylinder. A poor Transfer Efficiencyresults in excessive loading of fibres on cylinder, which restricts the furtherscope of card for improving the quality and increasing the production level.But the higher TransferEfficiency need not be taken as a measure of good carding. The cylinder load consists of two parts viz-basic load and working load. Thebasic load represents the fibres, which get absorbed into the cylinderfoundation over a period of time. And the working load represents fibre loadon surface from which fibre get transferred to the doffer. In the metallic cardsfibres on the surface constitute the cylinder load. A high cylinder load isnaturally determined to good carding. Since it enter fares with fibreseparation and individualization in cylinder flat region. Transfer Efficiency of card is very sensitive to some of the settings in card. Transfer Efficiency or Transfer Ratio is going to change not only frommachine to machine but also due to some machine parameters, like speed,settings, card clothing etc.When ordinary card clothing is used the Transfer Efficiency is about 5%. Nowa day with metallic wires being introduced, the Transfer Efficiency isenhanced up to 25%. This is because the loading and unloadingcharacteristics of the card vary with the flexible wire and metallic wire.A high cylinder load is naturally determined to good carding since it interfereswith fibre separation and individualization in cylinder flat region. Low transferefficiency is also undesirable, as it not only leads to building up of highercylinder load but also over working of fibres since poor transfer efficiencyresults in the fibres being taken round the cylinder more number of timesthan necessary and it causes nep generation.
"Transfer Efficiency is defined as the percentage of fiber transferred to dofferfrom cylinder per revolution of cylinder." The Transfer Efficiency of card is important from the point of view of determining the level of loading of the cylinder. A poor Transfer Efficiencyresults in excessive loading of fibres on cylinder, which restricts the furtherscope of card for improving the quality and increasing the production level.But the higher TransferEfficiency need not be taken as a measure of good carding. The cylinder load consists of two parts viz-basic load and working load. Thebasic load represents the fibres, which get absorbed into the cylinderfoundation over a period of time. And the working load represents fibre loadon surface from which fibre get transferred to the doffer. In the metallic cardsfibres on the surface constitute the cylinder load. A high cylinder load isnaturally determined to good carding. Since it enter fares with fibreseparation and individualization in cylinder flat region. Transfer Efficiency of card is very sensitive to some of the settings in card. Transfer Efficiency or Transfer Ratio is going to change not only frommachine to machine but also due to some machine parameters, like speed,settings, card clothing etc.When ordinary card clothing is used the Transfer Efficiency is about 5%. Nowa day with metallic wires being introduced, the Transfer Efficiency isenhanced up to 25%. This is because the loading and unloadingcharacteristics of the card vary with the flexible wire and metallic wire.A high cylinder load is naturally determined to good carding since it interfereswith fibre separation and individualization in cylinder flat region. Low transferefficiency is also undesirable, as it not only leads to building up of highercylinder load but also over working of fibres since poor transfer efficiencyresults in the fibres being taken round the cylinder more number of timesthan necessary and it causes nep generation.
Simpson's Analysis:
The doffer collecting fraction i.e. the proportion of fibre transferred to dofferdepends upon the following ratio of wire angles i.e.R = (Sinβ2 + Cosβ2)/ (Sinβ1 + Cosβ1)
β1 = inclination angle of cylinder wire point.
β2 = inclination angle of doffer wire point. This ratio reaches its maximum value 1.414 when β1 =90° and
β2=45°.
However, since a cylinder wire point angle of 90° would not given a goodcarding action, angle of 88° for cylinder and 45° for doffer are suggested.
Keeping production rate constant, if doffer speed is enhanced with aproportionate reduction in sliver hank the load on cylinder decreasesand Transfer Efficiency increases. It means at the same production ratea combination of faster doffer and lighter sliver improves carding.An increase in cylinder speed reduces load on cylinder. An increase incylinder speed the load on cylinder reduces with a concomitantincrease in transfer coefficient.In the first case, in order to keep the production rate constant, thedoffer speed needs to be adjusted according to sliver linear density. This however changes cylinder doffer surface speed ratio since cylinder speed remains unaltered.
In the Second Case, to keep the cylinder doffer surface speed ratioconstant, the cylinder speed is also changed in proportion to change indoffer speed. From above discussion it can be concluded that heaviersliver increases loading and decreases transfer efficiency. It had beenalso observed the load to be more for heavier sliver than the lighterone irrespective of production rate. Transfer efficiency was alwayshigher for lighter sliver.
An increase in production rate through doffer speed results in increasein loading and as well as transfer efficiency. It means even thoughtransfer efficiency increases, it does not increase proportionate toincrease in production rate, resulting cylinder load to increase.
Transfer Efficiency increases with closer setting cylinder doffer setting.Cylinder loading to decrease and transfer coefficient to increase withcloser setting since it increases the zone of interaction betweencylinder and doffer.If the diameter of doffer is reduced by half, the zone of interaction isreduced by 0.7 and the coefficient of entrapment by 1.18. Hencereduction in size may increase cylinder load. A higher wire point
density on doffer will reduce cylinder load. Though cylinder loadreduces with enhancement of wire point density on doffer but theeffect is less critical than wire angle.
Chiefly, carding should separate the flocks into
individual fibers. Additionally, carding results in cleaning, reduction
of neps, aligning, blending, and elimination of some short fibers. The
elimination of short fibers must, however, be viewed in proportion.
The main eliminated material is in the flat strips.
Assuming flat waste at 1 to 2%, with about half in the form of short
fibers there is such a minor precentage of short fiber elimination that
it could hardly be measured with the current coarse staple measuring
equipment. The operation of carding is performed with the aid of oppositely disposed sets of teeth or small wire hooks.
The
teeth face in opposite directions (Fig. 16). This is the typical
arrangement between the main cylinder and the flats, and also between
the main cylinder and the doffer. In order to enable carding to take
place, v1 must be greater than v2 or v2 must be in the opposite direction to v1. In this action, the fibers are drawn apart, separated, and aligned.
The
teeth of both clothing surfaces face in the same direction (Fig. 17).
This arrangement is typical of the licker-in/main cylinder region. Here
there is a deliberate transfer of material from one clothing surface to
another, but v1 must be greater than v2 (feeding clothing).
.
If a fiber is held by friction at its ends on two teeth that are moving apart, tensile forces F act
on the fiber in the axial direction owing to the drag from both sides
(Fig. 18). Since the fibers are held on inclined surfaces, this tensile
force can be resolved in accordance with the parallelogram of forces
into two easily derivable components E and K, E being
the component tending to draw the fibers into the clothing. The
retention capability of the clothing is dependent on this component. The
parameter K is the carding component, which presses
the fiber towards the points of the other clothing surface. The fibers
are in close contact with the other clothing surface and are processed
intensively.
Centrifugal force is superimposed on the forces produced
by the machine parts. However, in order to produce noticeable effects,
substantial speeds are required, and these speeds arise practically only
at the main cylinder and to some extent at the licker-in.
The centrifugal forces are effective mainly in
directions away from the main cylinder, and act both on fibers and on
foreign particles. In spite of this, the fibers are not thrown off (at
least the longer ones), because the high air resistance due to the
rotation presses the fibers back flat against the surface of the main
cylinder. In comparison to all other forces, centrifugal forces are of
minor significance except when considering trash and short fibers. In
this case the centrifugal forces support the transfer of trash and short
fibers from the main cylinder into the Flats.
Reference to the forces exerted by the teeth in the
carding disposition will show that, all other things being equal, it is a
matter of chance on which tooth tip the fiber will remain caught.
Such a random result is not acceptable everywhere. The
doffer, although it is in the carding disposition relative to the main
cylinder, must be able to take up a portion of the fibers. This is only
possible if the doffing conditions are improved by the following:
- An increased tooth density in the doffer clothing (no longer used with rigid wire clothing).
- A clothing supporting the carding capacity, by using a greater carding angle for the doffer clothing and thus obtaining an increased drawing-in component E.
- Maintaining the catching effect of the clothing by frequent sharpening.
- Keeping the doffer clothing clean and receptive by continually withdrawing the web.
- A very narrow setting between main cylinder and doffer.
- Assisting transfer of fibers by special air-circulation conditions in the convergent space between the main cylinder and the doffer.
Even with these measures, the odds in favor of transfer are not even 50:50.
According to Artzt and Schreiber , the transfer factor with rigid wire clothing is only 0.2-0.3.
This means that, on average, a fiber rotates from three
to five times with the main cylinder before it passes to the doffer. The
effect is caused by the strong adherence of the fibers to the main
cylinder, the fibers being drawn into the main cylinder clothing during
continual movement past the flats
This is the most serious problem zone of the card
because the licker-in must tear individual flocks out of the fairly
thick feed sheet with enormous force. Fiber damage is scarcely to be
avoided here.
However, stress on the fibers is not the only important
aspect. The degree of opening, on which the quality of carding is
directly dependent, is also important – the more so, the higher the
production rate of the card.
The degree of opening, degree of cleaning and, above all, damage to the raw material can be influenced by:
- thickness of the feed sheet;
- density of the feed sheet;
- evenness of the feed sheet;
- throughput speed;
- rotation speed of the cylinders;
- cylinder clothing;
- form of the feed plate;
- arrangement of the feed plate (co-rotation or counter-rotation).
On the other hand, the licker-in is the main elimination zone for coarse impurities.
The main work of the card, separation into individual
fibers, is performed between the main cylinder and the flats. Only by
means of this fiber separation is it possible to eliminate the last
dirt, especially the finer particles and dust. These pass into the
flats, the extraction system, or the droppings.
When a flat moves into the working zone, it first fills
up. This occurs relatively quickly, i.e. after only a few flats have
moved into the working zone. Thereafter, hardly any further take-up of
fibers occurs, and only carding takes place. Accordingly, if a fiber
bundle does not find a place in the first few flats, then it can be
opened only with difficulty.
It will be rolled between the working surfaces and usually leads to nep formation.
Equally important at this working position is the reduction of neps. Kaufmann indicates that 75% of all neps can be disentangled, and of these about 60% are in fact disentangled.
Of the remaining 40% disentanglable neps:
- 30-33% pass on with the sliver;
- 5-6% are removed with the flat strips;
- 2-4% are eliminated with the waste.
The intensity of separation depends on:
- the sharpness of the clothing;
- the spacing of the main cylinder from the flats;
- the tooth density of the clothing;
- the speed of the licker-in (high, but not too high);
- the speed of the doffer (high, but not too high).
The
arrangement of the clothing between the main cylinder and the doffer is
not, as might have been expected, a stripping arrangement, but a
carding arrangement. This is the only way to obtain a condensing action
and finally to form a web. It has both advantages and disadvantages. The
advantage, is that an additional carding action is obtained here. This
is important, since the processing of the fibers differs somewhat from
processing at the flats.
A disadvantage to be noted is the formation of hooks at
this point. Before transfer, some of the fibers remain caught at one end
on the teeth of the main cylinder (Fig. 22, T). During
transfer, the other ends of the projecting fibers are caught by the
clothing of the doffer and taken up. Since, however, the velocity of the
main cylinder is much higher than that of the doffer, the teeth of the
cylinder wire (T) smooth out the fibers in the
direction of rotation, whereby the rear ends of the fibers remain caught
on the teeth of the doffer (A).
By this means, they form hooks at their ends. In the
web, and then in the card sliver, most of the fibers in the strand
possess trailing hooks. However, aside from the serious disadvantage of
hook formation, the carding effect mentioned is also produced here,
since either the main cylinder clothing rakes through the fibers caught
in the doffer clothing, or the doffer clothing rakes the fibers on the
main cylinder. Neps can still be disentangled here, or non-separated
neps disentangled during the next passage through the flats
The intensity of carding (as at other carding positions) is here dependent upon
- type of clothing;
- geometry of the teeth;
- number of teeth per surface;
- distance between the carding surfaces;
- speed relationships;
- sharpness of the clothing;
- degree of wear of the clothing.
A disadvantage of web
formation at the card that has already been mentioned is the formation
of hooks. According to investigations by Morton and Yen in Manchester,
UK, and others, it can be assumed that the fibers in the web show the
following hooks:
- more than 50% have trailing hooks;
- about 15% have leading hooks;
- about 15% have doubled hooks,
- and less than 20% have no hooks.
Such
fiber hooks, which effectively convert longer fibers to short fibers,
cannot be permitted in the yarn. They must therefore be removed before
yarn formation. This is done by the draft or by combing as the following
description shows:
In the drafting arrangement, the fiber hooks may be
bedded in the body of fibers either as leading or as trailing hooks
(Fig. 23 and Fig. 24). Consider first a trailing hook (S):
it will be seen that for a certain period it moves with the remainder
of the fiber strand at the speed of the back roller towards the front
roller. If the fiber tip passes into the nip region of the drawing
roller, the fiber is accelerated. However, since the trailing end is
moving with a relatively thick body of slowly moving fibers, the fiber
is straightened before the whole fiber can reach the drawing speed — the
hook is eliminated. On the other hand, leading hooks (K)
are immediately caught bodily by the front roller and carried along
unchanged (Fig. 24). The comber however mainly straightens out leading
hooks, because the needles of the circular comb can grasp only these
(Fig. 25).
To eliminate the hooks,
leading hooks must be presented to the comber and trailing hooks to the
ring spinning machine. As Fig. 26 and Fig. 27 show, reversal of the hook
occurs at each processing stage between the card and these machines.
Accordingly, a definite number of machine passages are required in
intervening stages. Between the card and the comber, there must be an
even number of passages, and there must be an odd number between the
card and the ring spinning machine. In rotor spinning, the disposition
of the hooks is of little significance.
- Fig. 27 – Reversal of the dispositions of hooks between the card and the ring spinningIn cleaning, it is necessary to release the adhesion of the impurities to the fibers and to give particles an opportunity to separate from the stock. This is achieved mostly by picking flocks out of the feed material and by rapid acceleration of these flocks over a grid. Dirt, dust, foreign matter, and neps should be eliminated.Cleaning was always an important basic operation, and it will become steadily more important. For one thing, owing to machine harvesting, cotton contains more and more impurities, which furthermore are shattered by hard ginning; for another, almost all new spinning processes impose substantially higher demands on the cleanliness of the material than the conventional methods.
The available possibilities for cleaning natural fibers can be divided broadly into three groups:
- chemical cleaning;
- wet cleaning (washing);
- mechanical cleaning.
This
discussion will be confined to mechanical cleaning, in which usually
only particles on the surface of the flocks can be removed.
The following procedures can be used:
- striking = falling out;
- beating = ejecting;
- scraping = separation;
- suction = separation;
- combing = extracting;
- use of centrifugal force = ejecting.
Striking, carried out by pins, noses, etc., on the
Type and degree of openingopening devices<//a>,
leads to repeated collisions of the flocks with the grid-bars, causing
foreign particles to drop through. In a beating operation, the flocks
are subjected to a sudden strong blow. The inertia of the impurities,
accelerated to a high speed, is substantially greater than that of the
opened flocks owing to the low air-resistance of the impurities. The
latter are hurled against the grid and, because of their small size,
pass between the grid-bars into the waste box, while the flocks continue
around the periphery of the rotating beater. Impurities can be scraped
off when the fibers are guided, under relatively high friction, over
machine components, grid-bars, mote knives, or even other fibers.
This operation is chiefly of importance in dust removal.
Suction is less suited to the elimination of coarse particles than to
extraction of dust. Transport air is fed through filters or perforated
sheets; the small dust particles, which have been released during
beating or transport, pass with the air through the fine openings. The
flocks cannot pass.
In combing, needles pass completely through the body of
fibers and draw impurities out of the inner regions. This is the only
form of mechanical cleaning in which regions other than simple surfaces
are cleaned.
Genuine exploitation of centrifugal force, in which
there is no need for beating, is achieved, for example, in the card.
Because of their high ratio of mass to surface, when compared with the
fibers, the dirt particles are thrown out into the flats while the
fibers are retained in the clothing by the air current. This system was
used still more intensively in the “air stream cleaner” from the former
Platt company (Fig. 28). In this machine the transport flow of air and
stock (A) was subjected to rapid acceleration (V) before the transport direction was sharply altered, i.e. by more than 90° (E).
The flocks were able to follow the diversion but the heavier impurities
flowed straight on through a slot in the duct into a waste box (C).
However, as impurities have become smaller and smaller
in recent decades, this system does not function any longer – it has
been abandoned.
Ignoring perforated surfaces and combs, separation of stock and
impurities is achieved by devices which let the impurities pass but
retain the stock. In most cases a grid (beneath the beater) is used, and
this can be additionally fitted with one or two mote knives in front of
the grid (Fig. 29). Grids can be made of perforated sheet (low
elimination effect); slotted sheet (low elimination effect); bars with
edges, arranged one after the other. A controlled influence on the
elimination effect can be obtained by means of grid and mote knives. The
intensity of cleaning depends on the spacing of the grid from the
opening device; the setting angle of the bars relative to the opening
device; the width of the gaps between the bars.
Cylinder wire(wire angle, height, thickness and population) flat tops specification licker-in wire specification doffer wire specification feed weight draft between feed roller and doffer cylinder grinding doffer grinding flat tops grinding cylinder, falt tops, doffer wire life Licker-in wire life Cylinder speed flat speed Licker-in speed setting between cylinder and flat tops setting between licker-in and feed plate setting between licker-in and undercasing elements like , mote knife, combing segment etc. setting between cylinder and doffer setting between cylinder and back stationary flats setting between cylinder and front stationary flats setting between cylinder and cylinder undercasing
Cylinder Wire And Cylinder Speed
Cylinder wire selection is very important, it depends upon cylinder speed, the raw material to be processed and the production rate. The following characteristics of cylinder wire should be considered.
»
wire angle
»
tooth depth
»
wire population
»
rib thickness
»
tooth profile
»
tooth pitch
»
tooth point
» overall wire height
Wire front angle depends on mainly cylinder speed and
coefficient of friction of raw material. Higher the cylinder speed, lower the
angle for a given fibre. The cylinder speed in turn depends upon the production
rate.
Higher production means more working space for the fibre is
required. It is the wire that keeps the fibre under its influence during
carding operation. Therefore the space within the wire should also be more for
higher production. Higher cylinder speed also increases the space for the
fibre. Therefore higher cylinder speed is required for higher production. In
the case of high production carding machines, the cylinder surface is very much
higher, therefore even with higher number of fibres fed to the cylinder; the
cylinder is renewing the carding surface at a faster rate.
Higher the cylinder speed, higher the centrifugal force
created by the cylinder, this tries to eject the fibre from the cylinder, along
with the trash. It is the cylinder wire's front angle which overcomes the
effect of this force. Low front angle with too low cylinder speed and with high
frictional force will result in bad quality, because the fibre transfer from
cylinder to doffer will be less. Hence recycling of fibres will take place, which
result in more neps and entanglements. The new profile with less free blade
avoids loading of the cylinder with fibre and/or trash. This helps in keeping
the fibers at the tip of the tooth. The movement of the fibres towards the tip
of the tooth coupled with centrifugal action demands an acute front angle to
hold the fibre in place during carding.
Lack of stiffness associated with fine and/or long fibres
necessitates more control during the carding process. This control is obtained
by selecting the tooth pitch, which gives the correct ratio of the number of
teeth to the fibre length. Tooth pitch reduction is therefore required for exceptionally
short fibres and those lack stiffness.
Number of points across the carding machine is decided by
the rib width. It is selected based on the production rate and fibre
dimensions. Finer the fibre, finer the rib width. The trend is to finer rib
width for higher production.
The population of a wire is the product of the rib thickness
and tooth pitch. The general rule is higher populations for higher production
rates, but it depends upon the application. Sharp
tooth points penetrate the fibre more easily and help to intensify the carding
action. Cut-to-point wires are sharp and they have no land at all. The effective working depth of a cylinder wire
tooth for cotton is approximately 0.2mm and for synthetic materials
approx.0.4mm. Manmade fibres require more space in their cylinder wire than cotton.
More tooth depth allows the fibre to recycle, resulting in damaged fibres and
neps. If tooth depth is insufficient, there will be loss of fibre control. This
will result in even greater nep generation. Looking into the above details, the
following specifications can be used as a guideline.
MATERIAL
|
PRODN. RATE
|
RIB WIDTH
|
ANGLE(degrees)
|
POPULATION
|
Cotton low grade
|
low
|
0.6
|
65
|
700
|
Cotton low grade
|
high
|
0.5
|
55
|
840
|
Cotton Medium
|
low
|
0.6
|
60
|
800
|
Cotton Medium
|
high
|
0.4 to 0.5
|
55
|
840 to 950
|
Cotton fine
|
low
|
0.5
|
60
|
840
|
Cotton long
|
high
|
0.4 to 0.5
|
55
|
900 to 1100
|
Synth.coarse
|
low
|
0.7 to 0.5
|
70
|
550 to 650
|
synth.coarse
|
high
|
0.6
|
65
|
760
|
Synth.medium
|
low
|
0.7
|
65
|
700
|
synth.medium
|
high
|
0.5
|
65
|
760
|
Synth.fine
|
low
|
0.6
|
65
|
700
|
synth.fine
|
high
|
0.5
|
60
|
840
|
MATERIAL
|
PRODCUTION RATE
|
CYLINDER SPEED
|
cotton
|
low
|
360 to 400
|
cotton
|
medium
|
430 to 470
|
cotton
|
high
|
500 to 550
|
synthetic
|
low
|
300
|
synthetic
|
medium
|
380
|
synthetic
|
high
|
460
|
Doffer, Licker-In and Flat Tops:
The basic function of doffer is to strip the fibers from
Cylinder. Please remember that the action between cylinder and doffer is
carding action (or combing action or point to point action). The doffer wire's
front angle plays a very important role in releasing the fibre from the cylinder.
For most carding applications the optimum angle is 60 degrees.
Increased population over 400 ppsi does not give any
advantage in the production of quality yarn. For smaller doffers, 5 mm doffer
wire height helps in transferring the fibres from cylinder to doffer. If the
fibre holding capacity of the doffer wire is less due to fibre friction or due
to very high doffer speed, it is better to use a doffer wire with striations.
For high production carding it is always better to use doffer wire with
striations.
Licker-in plays a major role in opening the fibre tufts. In
general 85 degrees is used both for synthetic and medium and long cottons. For
coarse and dirty cottons 80 degrees can be used. Strength, hardness and
sharpness are very important for Licker in wire. Licker-in wires should never
be ground. Thinner blades penetrate the fibres more efficiently and increase
the wire life.
Higher number of rows per inch gives better results. Now up
to 12 rows per inch is being used. This is always better compared to 8 rows per
inch. If the wire pitch is not sufficient, it can be compensated by increasing
the licker-in speed. Higher licker-in speeds for fine and long cottons will
rupture the fibres. Licker-in speed depends upon the fibre type and the
production rate.
It is better to use a flat top with more than one
population. The general combination is 280/450.This is suitable for both cotton
and synthetics. Please remember that the rigidity of the fillets is different
for cotton and synthetic. If cotton flat tops are used for synthetic
processing, the load on the cylinder will be more, more heat will be produced
and hence the probability of cylinder loading due to electrostatic charge will
be high. Instead of using Rigid type flat tops, it is better to use semi-rigid
type flat tops while processing synthetic fibres.
Settings:
The setting between cylinder and doffer is the closest
setting in the card. This setting mainly depends upon the cylinder speed, hank
of the delivered sliver and the type of wire. Cylinder speed upto 360, the
setting should be 0.1mm. For cylinder speeds more than 450, the setting ranges
from 0.125 to 0.15.If the setting between cylinder and doffer is very close,
the wires will get polished and this will affect the fibre transfer. If the
setting is too wide, the fibres will not be transferred to doffer from the
cylinder, hence cylinder will get loaded. While processing synthetic fibres cylinder
loading will badly affect the yarn quality. Moreover, it is difficult to
improve the wire condition if the loading is severe. The only solution would be
to change the wire. Therefore enough care should be taken while processing
synthetic fibres.
The most critical setting in a carding machine is between cylinder and flat tops. While processing cotton, it can be as close as 0.175 mm provided the mechanical accuracy of flat tops is good. Since most of the cards are with stationary flats at the licker-in side, the setting from the back to front for flats can be 0.25, 0.2, 0.2, 0.2, 0.2mm.
Closer the setting between cylinder and flats, better the
yarn quality. Neps are directly affected by this setting. Of course, very close
setting increase the flat waste. For processing cotton the setting can be 0.25,
0.2, 0.2, 0.2, 0.2mm. For synthetic fibres it can be 0.3, 0.25, 0.25, 0.25,
0.25mm. Most of the cards are with 6 to 11 stationary flats at the licker-in
side. This setting can start with 0.4 mm and end with 0.25mm. The wire points
can start with 140 ppsi and end with 320 ppsi. The work done by the first few
stationary flats is very high, therefore the wear of these flats is also high.
It would be better if the first 50% of the flats are changed after 100000 kgs
of production and the rest after 150000 kgs of production. These stationary
flats open the material so that, the setting between cylinder and flats can be
as close as possible.
The setting between feed plate and Licker-in depends upon
the type of feed plate. Conventional feed plate setting is decided mainly by the feed weight and to some extent by
the fibre length and type. With the latest feed plate and feed roller
arrangements, the setting is decided mainly by the fibre length and to some
extent by the feed weight.
Normally the setting between the feed plate and Lickr-in is
around 0.45 to 0.7mm, depending upon the feed weight and fibre type. The
setting between Licker-in and the first mote knife is around 0.35 to 0.5 mm.
This helps to remove the heavier trash particles and dust. Closer the setting,
higher the waste percentage. The setting between Licker-in and combing segments
is around 0.45 to 0.6. This helps to open the material.
Some cards have two mote knifes in the Licker-in
undercasing. The setting is around 0.4 to 0.5mm. This helps to remove the
smaller trash and dust particles.
The setting between the cylinder and stationary flats at
Doffer side helps to transfer the fibres to doffer by stripping the fibres to
the top of the cylinder wire. This setting can be as close as 0.15mm. Number of
wire points on stationary flats also plays major role. It is normally around
300 to 400. For a high production application it can be as high as 600. For
cotton processing, the stationary flats are fixed with a knife attachment. The
setting should e as close as possible, i.e. around 0.15mm. This helps to remove
the trash particles of very small size.
The setting between cylinder and cylinder undercasing should
be as per the manufacturer's recommendation. The design of undercasing is
different for different manufacturers. This setting is very important, as wrong
settings will affect the fibre transfer and can also create air turbulance.
Speeds:
Higher cylinder speed helps fibre transfer. Higher the
production, higher should be the cylinder speed. Higher cylinder speed improves
carding action, thereby imperfections are reduced. Higher Licker-in speed for
coarse fibres and diry cotton helps to remove the trash and improves, better
the yarn quality. For fine and long cottons, higher speed results in fibre rupture,
therefore, flat waste and comber noil will be more.
Higher flat speed improves yarn quality and at the same time
increases the flat waste. With the same flat speed, higher the carding production,
lower the flat waste and vice-versa. Very high tension drafts will affect
carding U%. It is better to keep the draft between feed rollers to doffer
around 75 to 95. The results are found better with these drafts.
Wire Maintenance:
For a modern cylinder wire of 2mm height, grinding with the
normal grinding stone is not recommended. It is better to use TSG grinder from
GRAF. It is better to grind the wire every 2nd or 3rd month, so that the
sharpness of the wire is always maintained.
TSG grinder does not grind the wire, therefore if the wire
is worn out very badly the quality improvement using this grinding machine will
be nil. Frequent grindings are recommended. If TSG grinder is not available, it
is better not to grind 2mm wires. The number of traverse should increase
depending upon the life of the wire. The number of traverse for successive
grindings should be like this 3, 5, 10,17 etc. Anyway the best method is to
confirm with the microscope. If the grinding is not sufficient, the number of
traverse should be increased.
Doffer is still working with a concept of Land formation. A
normal grinding machine will be good for doffer grinding. All the wire points
should be touched by the grinding stone. A slow and gradual grinding with the
grind-out concept will give the best results. Harsh grindings will result in
burr formation on the land. This will increase the number of hooks in the
fibre, thereby the effective length of the fibre from this card will be
reduced.
Flat tops grinding is very important. Every time a flat top
is ground, yarn quality is improved. It is better to use a grinding machine
with the emery fillet. Frequent flat tops grinding will result in less neps and
the yarn quality will be consistent. Some mills increase the life of the flat
tops compared to cylinder wire. But it is better to change flat tops and
cylinder wire together for better and consistent yarn quality.
It is a good practice to check the individual card quality
before changing the wire. Licker-in wire should be changed for every 150000
kgs. Earlier changes will further improve the yarn quality. Stationary flats
should be changed for every 150000 kgs. But it is a good practice to change the
first 3 or 6 stationary flats at Licker-in side for every 100000 kgs. This
helps to maximise the carding effect between cylinder and doffer which is
critical for better yarn quality.
Others:
Lower the feed variation, better the carding quality. Even
if the card is with an autoleveller, feed variations should be kept as low as
possible (plus or minus 10%). With the latest chute feed systems, it is easy to
control the feed variation with in 5%. Lower the feed variation, lower the
draft deviation, therefore yarn quality will be consistent.
If the card is with autoleveller, the nominal draft should
be selected properly. Improper selection will affect sliver C.V% and yarn
quality.
Improper feed roller loading and the setting between feed
roller and feed plate will affect the quality, especially C.V% and neps. Before
mounting, the eccentricity of cylinder and doffer should be checked. Eccentric
cylinder and doffer will affect the U% and will affect C.V. % also. Defective bearings,
gears and timing belts will affect U%. Uneven distribution of tension drafts
will affect U%.
Selvedge of feeding bat should be good. It should not be
folded and double. This will increase the neps and sometimes it may result in
cylinder loading. Lap fed to the carding machine should be narrower than the
nominal width of the machine. For processing cotton, minimum 800 pascal suction
pressure should be maintained at trash master (at knife) for effective removal
of trash and dust particles. Worn or damaged scraper blades will lead to web
sticking to crush rollers. Insufficient pressure between scraper blade and
crush roller will also result in web sticking. If the calender roller pressure
is too high web sticking will also be high.
If
Cylinder undercasing nose at
doffer side is too long for the type of fibre being carded web
disappearing problem will arise. If the nose is set too close to the
cylinder, web disappearing problem will arise. Damaged and dull doffer
wire also will result in web disappearing problem.
Key Features of Trützschler TC-11 Card are:
- Fully-integrated tuft feeder DIRECTFEED- High production with even card feeding
- Setting Optimiser T-Con - For maximum utilisation of the TC 11 potential
- Flexible Integral Feed Tray SENSOFEED+/- - Short-wave levelling for a low sliver count variation
- Sliver former WEBSPEED - Completely maintenance-free
- Precision Knife Setting System PMS - Adjustment of waste amount in no time at all
- Aluminium flat bars without screw connection - Quick flat exchange, without tools
- Magnet Flat System MAGNOTOP - Replacement of flat tops directly on the machine without tools
- Precision Flat Setting System PFS - Reproducible flat setting in only a few seconds
- Flat Measuring System FLATCONTROL - Objective and very precise flat adjustment
- Infinitely variable setting of the flat speed - Exact adaptation to the fibre quality in only a few seconds
- Electronic cylinder brake - Reduces cleaning and maintenance time
- Nep sensor NEPCONTROL - Online measurement of neps and trash particles
- Computer control with touch screen - Simple operation and targeted maintenance
- Digital motor controls - Maintenance-free and high-precision
- Spectrogram monitoring - Stops the card in case of faults in the spectrogram
- Thick place monitoring - Stops the card in case of excessive thick places in the sliver
- Spectrogram analysis - Assists in finding the cause of spectrogram errors
- Management of maintenance and card clothing - Targeted maintenance support
- 3-roll WEBFEED Unit - For gentle pre-opening
- WEBFEED with one roll - For the carding of man-made fibres or ELS cotton
- Needle or clothed rolls - Perfectly tailored to your product
- Thick place monitoring and metal detection in the feed area - For quality assurance and protection of the card
- Long- and short-wave levelling system - For perfect card sliver evenness
- Special toothed belts for flat guiding - Flat replacement without tools
- Premium clothings from TCC, made of high-grade steel - Extended service life ensures longer maintenance intervals
- High-precision aluminium elements with super-smooth surfaces - Gentle material guidance in the fibre-carrying areas
- Central safety locking system - High operational safety
Unique features of the TC 15 in the high-performance segment are:
- Expansion of performance limits through T-MOVE and T-CON
- Increased delivery speeds during can change (can diameter 1,000 mm and 1,200 mm)
- Reduced air consumption
- Smallest floor space in comparison to production
- Lowest waste quantities
New web doffing
Today's technology allows delivery speeds well above 400 m/min in practice. For this reason, web doffing and sliver forming have been newly developed for speeds up to 500 m/min for the TC 15.Quality at the highest level
"The length of the carding section determines the quality". Even though this has been common knowledge for some time, Trützschler is the only one with the longest carding section worldwide. For this reason, Trützschler cards have set the standard for quality for decades. The valuable raw material cotton is optimally used, which ultimately also contributes to an increase in productivity.C 70 High-performance card - The card with the maximum active carding area
The C 70 high-performance card achieves excellent quality values at highest production for all yarn applications. This is based on the well-proven 1.5 m working width and maximum active carding area. Precise flats guiding and innovation in the pre- and post-carding area allow, with the selective waste extraction, an excellent raw material exploitation and sliver quality. With the integrated grinding system IGS, the sliver quality is maintained at a high level. By utilising draw frame modules instead of the classical can coilers, the customer has the possibility to optimally layout the process.Economy
- High production performance with top quality for all yarn applications thanks to the maximal active carding area and optimised pre- and post-carding area.
- Excellent raw material exploitation thanks to the adjustable knife on the licker-in, variable insertions of the extraction elements in the pre- and post-carding area as well as to the electronically adjustable flat speed.
- The lowest energy balance of the C 70 is based on the combination of compact construction with small, movable masses and innovative machine geometry and flats area.
Quality
- IGS – ensures a consistently good sliver quality with permanently sharp clothings and therefore increases the service life of clothings.
- High production and sliver quality with the reliable autolevelling of the card and controlled fibre transport.
- Sophisticated detailed solutions for absolutely uniform batt weight and web formation give a card sliver of superior quality and lead to machine operation requiring no intervention.
Flexibility
- The modular construction permits a rapid adjustment to new raw materials and requirements.
- The draw frame modules facilitate an optimal process, adjusted to raw material and application.
- The option exists to arrange the card lines with 8 cards, line production up to 600 kg/h or with 10 C 70 cards, line production up to 1 200 kg/h.
The new Rieter C 70 high-performance Card
With the C 70, Rieter has succeeded in
raising the dependable technology of the 1.5 m wide card to a new
level. Basis for the improvement in production and quality is the
enlarged active carding area in combination with the precisely
controllable carding gap. Optimized extraction elements in the pre- and
post-carding area lead to a high raw material utilization. This raw
material utilization and the lower energy consumption per kilogram of
card sliver contribute to the efficient production of superior quality
yarn.
Enormous leap in productivity
The production performance of the C 70 card, compared to that of the C 60, can be increased by up to 40% with equal or better sliver quality. This marked improvement is achieved by redistributing the carding zones in the flats area and by redesigned flats guiding.Key factor, carding area
With the C 70, 32 flats are operative. Compared to the C 60, the active flats area is increased by 45% and compared to a conventional card by 60%. This means that with each cylinder clothing of the C 70, distinctly more carding work is performed.Quality through precise carding gap
The precise flats guiding and the revised flats design permit a very exact and reproducible setting of the distance between the cylinder clothing and the flats, so that a minimum of 0.1mm is possible. This precision leads to improved carding results. Furthermore, the flats cleaning of the C 70 has been completely reorganized.Optimal raw material exploitation
The customer profits from an optimal fiber utilization thanks to the extraction knife in the pre- and post-carding area. The extraction knife with variable ejector distance can be exchanged without tools in the shortest possible time.The flats speed is infinitely adjustable via the frequency converter, independent of the cylinder speed. This means the card can be individually adjusted and thereby optimized to the type of raw material being processed.
Uniform sliver quality
The proven integrated cylinder grinding system IGS – an exclusive Rieter product – is available as an option and provides the customer with constant quality values during the whole lifespan of the card clothing. With this fully-automatic grinding system, downtimes for clothing maintenance are a thing of the past.Low energy consumption
The high production performance of the C 70 positively affects the energy consumption per kilogram of produced card sliver. The C 70 has a 15% lower energy requirement than that of the C 60 which, considering the globally rising prices of electricity, represents a principal factor in the economic production of yarn.
CARD LC636
SALIENT FEATURES
- Higher Production up to 250 kg/hr
- Working width of 1,500 mm
- Pressure regulated chute for better feeding
- Specialized profiled finger plate
- Opening roller with mote knife for trash ejection
- Special stripper roller with tangential air strips for effective
feed to card - Individual drive for feed, opening and stripper rollers
- Direct feeding to card feed roller
- Single Licker-in arrangement with Arcual combing segment
- Highest Active Carding Area of 1.95 m2
- Highest Active Cylinder Area of 3.95 m2
- Optimum cylinder diameter of 1,017 mm, leading to lower thermal expansion and higher centrifugal force
- Standalone 40” Linear Coiler
SALIENT FEATURES
- Higher Production, up to 120 kg/hr
- Triple / Single Licker-in arrangement
- Aluminium alloy flats with increased no. of revolving flats
- Highest Active Flat Index (AFI)
- Pressure Regulated Chute for Uniform Feeding
- Optimum waste extraction at right place
- Precision and balanced geometry of technological elements
- High take up web doffing device

Card LC363 / LC361 is designed for higher production up to 120 kg/hr with distinctivefeatures to produce high quality sliver in every variety of cotton, man-made fibre and blends.“Well carded is half spun”. Card LC363 / LC361 is configured to produce better yarncharacteristic with reduction in running cost.
PRESSURE REGULATED CHUTE
Pressure regulated chute ensures active compression on the fibre material resulting intooptimal batt structure for highest sliver quality.FEED AND LICKER-IN ZONE
Card LC363 / LC361 has unidirectional feeding arrangement with saw toothed feed rollerfor gripped and gentle fibre transfer to Licker-in zone. The material is fed from feed roller inthe direction of rotation of the Licker-in to eliminate the fiber rupture. Variable nippingdistance can be set for processing different staple fibres.The triple Licker-in system with high speed will provide more percentage of individualizedfibers. The 1st Licker-in has double knife and an Arcual combing segment for intensivecleaning and pre opening. 2nd and 3rd Licker-in has a replaceable combing strip for furthergentle opening. Optimised wires and Specialized Angle help reduce load to cylinder.Resulting in better carding action in cylinder zone.
Brians Club is a cc shop which sells credit & debit cards in exchange of Bitcoin
ReplyDelete