INDUSTRY 4.0
Industry 4.0—the Industrial Internet of Things (IIoT)
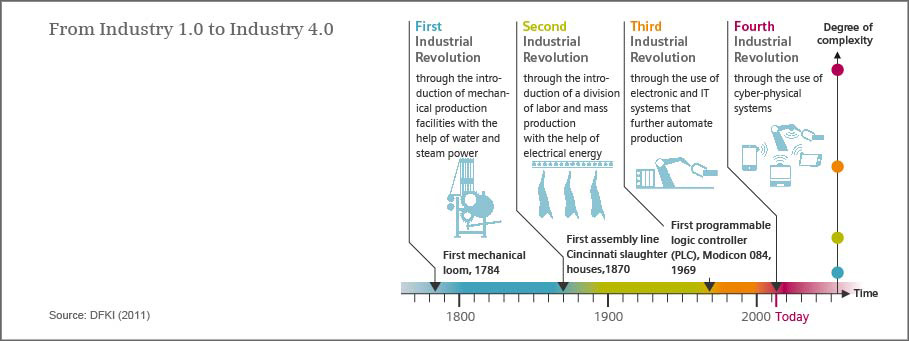

Embracing Industry 4.0 and Rediscovering Growth
The
rise of new industry oriented digital technology, known as Industry 4.0, is a
game changer that makes it possible to gather and analyze data across
machines, enabling faster, more flexible, and more efficient processes
to produce higher-quality goods at reduced costs. This manufacturing
revolution will increase productivity, shift economics, foster
industrial growth, and modify the interface of workforce.—ultimately changing the competitiveness of industry across regions.
The world of manufacturing is changing. To survive and thrive now,
you have to be willing to invest in Industry 4.0. This resource will
help you get started.
Evolution of Industry from 1.0 to 4.0
Before digging too much deeper into the what, why,
and how of Industry 4.0, it’s beneficial to first understand how exactly
manufacturing has evolved since the 1800s. There are four distinct
industrial revolutions that the world either has experienced or
continues to experience today.
The First Industrial Revolution
The first industrial revolution happened between the late 1700s and
early 1800s. During this period of time, manufacturing evolved from
focusing on manual labor performed by people and aided by work animals
to a more optimized form of labor performed by people through the use of
water and steam-powered engines and other types of machine tools.
The Second Industrial Revolution
In the early part of the 20th century, the world entered a second
industrial revolution with the introduction of steel and use of
electricity in factories. The introduction of electricity enabled
manufacturers to increase efficiency and helped make factory machinery
more mobile. It was during this phase that mass production concepts like
the assembly line were introduced as a way to boost productivity.
The Third Industrial Revolution
Starting in the late 1950s, a third industrial revolution slowly
began to emerge, as manufacturers began incorporating more
electronic—and eventually computer—technology into their factories.
During this period, manufacturers began experiencing a shift that put
less emphasis on analog and mechanical technology and more on digital
technology and automation software.
The Fourth Industrial Revolution, or Industry 4.0
In the past few decades, a fourth industrial revolution has emerged,
known as Industry 4.0. Industry 4.0 takes the emphasis on digital
technology from recent decades to a whole new level with the help of inter connectivity through the Internet of Things (IoT), access to
real-time data, and the introduction of cyber-physical systems. Industry
4.0 offers a more comprehensive, interlinked, and holistic approach to
manufacturing. It connects physical with digital, and allows for better
collaboration and access across departments, partners, vendors, product,
and people. Industry 4.0 empowers business owners to better control and
understand every aspect of their operation, and allows them to leverage
instant data to boost productivity, improve processes, and drive
growth.
Basic IIoT Concepts and Glossary of Terms
There are hundreds of concepts and terms that relate
to IIoT and Industry 4.0, but here are 12 foundational words and phrases
to know before you decide whether you want to invest in Industry 4.0
solutions for your business:
- Enterprise Resource Planning (ERP): Business process management tools that can be used to manage information across an organization.
- IoT: IoT
stands for Internet of Things, a concept that refers to connections
between physical objects like sensors or machines and the Internet.
- IIoT: IIoT
stands for the Industrial Internet of Things, a concept that refers to
the connections between people, data, and machines as they relate to
manufacturing.
- Big data: Big
data refers to large sets of structured or unstructured data that can
be compiled, stored, organized, and analyzed to reveal patterns, trends,
associations, and opportunities.
- Artificial intelligence (AI): Artificial
intelligence is a concept that refers to a computer’s ability to
perform tasks and make decisions that would historically require some
level of human intelligence.
- M2M: This
stands for machine-to-machine, and refers to the communication that
happens between two separate machines through wireless or wired
networks.
- Digitization: Digitization refers to the process of collecting and converting different types of information into a digital format.
- Smart factory: A smart factory is one that invests in and leverages Industry 4.0 technology, solutions, and approaches.
- Machine learning: Machine
learning refers to the ability that computers have to learn and improve
on their own through artificial intelligence—without being explicitly
told or programmed to do so.
- Cloud computing: Cloud
computing refers to the practice of using interconnected remote servers
hosted on the Internet to store, manage, and process information.
- Real-time data processing: Real-time
data processing refers to the abilities of computer systems and
machines to continuously and automatically process data and provide
real-time or near-time outputs and insights.
- Ecosystem: An
ecosystem, in terms of manufacturing, refers to the potential
connectedness of your entire operation—inventory and planning,
financials, customer relationships, supply chain management, and
manufacturing execution.
- Cyber-physical systems (CPS): Cyber-physical
systems, also sometimes known as cyber manufacturing, refers to an
Industry 4.0-enabled manufacturing environment that offers real-time
data collection, analysis, and transparency across every aspect of a
manufacturing operation.
Now that you have a better understanding of some of the core concepts
related to Industry 4.0, you’re ready to dig deeper into how smart
manufacturing can revolutionize the way you run and grow your business.
Smart Manufacturing Use Cases
One of the best ways to understand the concept of
smart manufacturing better is to think about how it could be applied to
your business, or a business similar to your business. Here are three
use cases that can help you understand the value of Industry 4.0 in a
manufacturing operation:
- 1. Supply chain management and optimization—Industry
4.0 solutions give businesses greater insight, control, and data
visibility across their entire supply chain. By leveraging supply chain
management capabilities, companies can deliver products and services to
market faster, cheaper, and with better quality to gain an advantage
over less-efficient competitors.
- 2. Predictive maintenance/analytics—Industry
4.0 solutions give manufacturers the ability to predict when potential
problems are going to arise before they actually happen. Without IoT
systems in place at your factory, preventive maintenance happens based
on routine or time. In other words, it’s a manual task. With IoT systems
in place, preventive maintenance is much more automated and
streamlined. Systems can sense when problems are arising or machinery
needs to be fixed, and can empower you to solve potential issues before
they become bigger problems. Predictive analytics allow companies to not
just ask reactive questions like, “what has happened?,” or “why did it
happen?,” but also proactive questions like, “what is going to happen,”
and, “what can we do to prevent it from happening?” These type of
analytics can enable manufacturers to pivot from preventive maintenance
to predictive maintenance.

3. Asset tracking and optimization—Industry 4.0
solutions help manufacturers become more efficient with assets at each
stage of the supply chain, allowing them to keep a better pulse on
inventory, quality, and optimization opportunities relating to
logistics. With IoT in place at a factory, employees can get better
visibility into their assets worldwide. Standard asset management tasks
such as asset transfers, disposals, re-classifications, and adjustments
can be streamlined and managed centrally and in real time.
NineTechnologies Transforming
Industrial Production
Advanced digital technology is
already used in manufacturing, but with Industry 4.0, it will transform
production. It will lead to greater efficiencies and change traditional
production relationships among suppliers, producers, and customers—as well as
between human and machine. Nine technology trends form the building blocks of
Industry 4.0.
1. BIG DATA AND ANALYTICS
What is it?
In
an Industry 4.0 context, the collection and comprehensive evaluation of
data from many different sources—production equipment and systems as
well as enterprise- and customer-management systems—will become standard
to support real-time decision making.
It
is the process of examining large and varied sets of data to uncover
hidden patterns, unknown correlations, market trends, customer
preferences and other information that’s useful to businesses.
What is the potential?
There are still massive amounts of untapped data in the industrial world. Their analysis will:
- optimise production quality
- save energy
- improve services
- allow real-time decision-making.
An industry example:
Semiconductor
manufacturer Infineon Technologies has decreased product failures by
correlating single-chip data captured in the testing phase at the end of
the production process with process data collected earlier. This allows
them to identify patterns that help discharge faulty chips early in the
production process and improve production quality.
2. AUTONOMOUS ROBOTS
What is it?
Manufacturers
in many industries have long used robots to tackle complex assignments
(think mechanical arms on assembly lines). But robots are evolving for
even greater utility, becoming more autonomous, flexible and
cooperative.
Robots will eventually interact with one another and work safely side by side with humans and learn from them. These robots will cost less and have a greater range of capabilities than those used in manufacturing today.
What is the potential?
Robots
will eventually interact with one another and work safely side by side
with humans - known as cobots. Eventually they will be able to learn
from humans.
An industry example:
Industrial
robot supplier, ABB, has launched a two-armed robot called YuMi® that
is specifically designed to assemble products alongside humans. It
includes flexible hands, parts feeding systems, camera-based part
location and state-of-the-art robot control.
3. SIMULATION
What is it?
Computer simulations have been used for years to determine the best possible design for production and distribution systems.
Simulations
will be used more extensively in plant operations to leverage real-time
data and mirror the physical world in a virtual model, which can
include machines, products, and humans. This will allow operators to
test and optimize the machine settings for the next product in line in
the virtual world before the physical changeover, thereby driving down
machine setup times and increasing quality.
What is the potential?
3D
simulation of product development, material development and production
processes will become widespread. Operators will be able to test and
optimise machine settings for the next product even before production
starts – reducing setup times and improving quality. Rapid testing in
the virtual world will ultimately lead to faster innovation in the
physical one.
An industry example:
Siemens
and a German machine-tool vendor developed a virtual machine that can
simulate the machining of parts using data from the physical machine.
This lowers the setup time for the actual machining process by as much
as 80 per cent.
4. HORIZONAL AND VERTICAL SYSTEM INTEGRATION
What is it?
With
Industry 4.0, companies, departments, functions, and capabilities will
become much more cohesive, as cross-company, universal data-integration
networks evolve and enable truly automated value chains.
Horizontal
integration means networking between individual machines, items of
equipment or production units. Vertical integration means gaining
control of different parts of the supply chain.
What is the potential?
An
entire organisation will be interconnected and companies will be
connected with one another. With Industry 4.0, companies, departments,
functions and capabilities will become much more cohesive and
cross-company, universal data-integration networks evolve and enable
truly automated value chains.
An industry example:
Dassault
Systèmes and BoostAeroSpace launched a collaboration platform for the
European aerospace and defence industry. The platform, AirDesign, serves
as a common workspace for design and manufacturing collaboration and is
available as a service on a private cloud. It manages the complex task
of exchanging product and production data among multiple partners.
5. THE INDUSTRIAL INTERNET OF THINGS
What is it?
Industry 4.0 means that more devices—sometimes including unfinished products—will be enriched with embedded computing. This
will allow field devices to communicate and interact both with one
another and with more centralized controllers, as necessary. It will
also decentralize analytics and decision making, enabling real-time
responses.
A
way of bringing together machines, advanced analytics and people at
work. It’s the network of a multitude of devices connected by
communications technologies that results in systems that can monitor,
collect, exchange, analyse and deliver valuable new insights.
What is the potential?
More
devices – sometimes even unfinished products – will be enriched with
embedded computing. This will allow field devices to communicate and
interact both with one another, and with more centralised controllers.
This will:
- improve connectivity
- improve efficiency
- save time
- save money through predictive maintenance, improved safety and other operational efficiencies
- enable real-time responses
An industry example:
Bosch
Rexroth, a drive-and-control-system vendor, outfitted a production
facility for valves with a semi-automated, decentralized production
process. Products are identified by radio frequency identification
codes, and workstations “know” which manufacturing steps must be
performed for each product and can adapt to perform the specific
operation.
6. CYBERSECURITY
What is it?
With
the increased connectivity and use of standard communications protocols
that come with Industry 4.0, the need to protect critical industrial
systems and manufacturing lines from cybersecurity threats
increases dramatically. As a result, secure, reliable communications as
well as sophisticated identity and access management of machines and
users are essential.
Utilised
by most businesses, cyber security is made up of technologies,
processes and controls that are designed to protect systems, networks
and data from cyber attacks.
What is the potential?
With
the increased connectivity and use of standard communication protocols
that come with Industry 4.0, cybersecurity has never been more
important. Sophisticated identity and machine access management systems
are essential for secure, reliable communications.
An industry example:
Worldwide
spending on the Internet of Things security will increase by 28 per
cent to $1.5 billion (£1bn) in 2018, according to Gartner, as
organisations become increasingly aware of the need to secure connected
devices.
7. THE CLOUD
What is it?
More
production-related undertakings will require increased data sharing
across sites and company boundaries. At the same time, the performance
of cloud technologies will improve, achieving reaction times of just
several milliseconds. As a result, machine data and functionality will
increasingly be deployed to the cloud, enabling more data-driven
services for production systems.
This
is a way of storing and accessing data and programs over the internet.
Cloud services that provide real-time information and scalability can
support a multitude of devices and sensors, along with all the data they
generate.
What is the potential?
More
production-related processes that require increased data sharing across
sites and company boundaries. At the same time, the performance of
cloud technologies will improve, achieving reaction times of just
several milliseconds. As a result, machine data and functionality will
increasingly be deployed to the cloud.
An industry example:
Manufacturers
are using the cloud to collaborate, not just internally, but with
suppliers and distributors. This allows them to move at a fast pace and
launch new products with more speed than ever.
8. ADDITIVE MANUFACTURING
What is it?
Companies have just begun to adopt additive manufacturing, such as 3-D printing,
which they use mostly to prototype and produce individual components.
With Industry 4.0, these additive-manufacturing methods will be widely
used to produce small batches of customized products that offer
construction advantages, such as complex, lightweight designs.
Otherwise
known as 3D printing, additive manufacturing is a technology that has
been around for at least three decades. It’s used to prototype and
produce individual components.
What is the potential?
It
will be widely used to produce small batches of customised products
that offer construction advantages, such as complex and lightweight
designs. High performance, decentralised systems will reduce transport
distances and inventory management costs.
An industry example:
Aerospace
companies are already using additive manufacturing to apply new designs
that reduce aircraft weight, lowering their costs for raw materials
such as titanium.
9. AUGMENTED REALITY
What is it?
Augmented-reality-based
systems support a variety of services, such as selecting parts in a
warehouse and sending repair instructions over mobile devices. These
systems are currently in their infancy, but in the future, companies
will make much broader use of augmented reality to provide workers with
real-time information to improve decision making and work procedures.
Currently
in their infancy, augmented reality-based systems support a variety of
services, such as selecting parts in a warehouse and sending repair
instructions over mobile devices.
What is the potential?
Companies
will make much broader use of augmented reality to provide workers with
real-time information to improve decision making and work procedures.
For
example, worker may receive repair instructions on how to replace a
particular part as they are looking at the actual system needing repair.
This information may be displayed directly in the worker’s field of
vision using devices such as augmented reality glasses.
An industry example:
The
U.S. army now uses ‘Tactical Augmented Reality’ (TAR). It’s basically
an eyepiece that enables soldiers to find the positions of friends and
enemies. TAR will eventually replace night-vision goggles, as it also
allows soldiers to see in the dark. It will also replace their handheld
SAT NAV systems. The system is entirely wireless. The eyepiece connects
to a tablet worn by the soldiers. It’s also connected to a thermal site
mounted on their rifles or carbines. If a soldier points a weapon, the
image of the target and details such as the distance to that target, are
seen through the eyepiece.
Artificial Intelligence ( AI)
Artificial intelligence (AI) is wide-ranging branch of
computer science concerned with building smart machines capable of performing
tasks that typically require human intelligence. AI is an
interdisciplinary science with multiple approaches, but advancements in Machine
Learning and deep
learning are creating a paradigm shift in virtually every sector of
the tech industry.
- AI automates repetitive learning and discovery through data. But AI is different from hardware-driven, robotic automation. Instead of automating manual tasks, AI performs frequent, high-volume, computerized tasks reliably and without fatigue. For this type of automation, human inquiry is still essential to set up the system and ask the right questions.
- AI adds intelligence to existing products. In most cases, AI will not be sold as an individual application. Rather, products you already use will be improved with AI capabilities, much like Siri was added as a feature to a new generation of Apple products. Automation, conversational platforms, bots and smart machines can be combined with large amounts of data to improve many technologies at home and in the workplace, from security intelligence to investment analysis.
- AI adapts through progressive learning algorithms to let the data do the programming. AI finds structure and regularities in data so that the algorithm acquires a skill: The algorithm becomes a classifier or a predictor. So, just as the algorithm can teach itself how to play chess, it can teach itself what product to recommend next online. And the models adapt when given new data. Back propagation is an AI technique that allows the model to adjust, through training and added data, when the first answer is not quite right.
-
-
Future of the textile jobs on the onset of Industry 4.0:
Globalization, demographic changes and adoption of Industry 4.0 are the three giant factors that will determine the future of jobs in the textile sector. The Industry 4.0 has created a major impact in the service sectors as well as retail marketing. However, the extent of its impact depends on the extent to which the industry adopts the new technologies including Robotic Process Automation, Artificial Intelligence, Machine Learning and Internet of Things.
In India, Industry 4.0 is still in its infant stage and its impact on the future of jobs can only be understood once the industry leaders experiment largely with these new technologies and showcase the benefits to the ret of the players.
The impact of Industry 4.0 will result in different possibilities. Some new jobs would be created, some existing ones would need additional skill requirements, some would continue to exist without any change while some would disappear. The jobs that would disappear are the ones that would require Routine Manual and Routine Cognitive skills. All such jobs would be automated.
Among the two sectors, textiles and apparels, the latter is more likely to adopt the new technologies because high labour intensive operations are required in stitching, packing and inspection. Job roles such as fabric checker, packer helper etc will most probably cease to exist.
Even before the introduction of Industry 4.0, the spinning sector had long gone replaced some of the job roles which required RM and RC skills with robotics. For example, auto doffers on ring frame, chute feed cards, etc.
The Textile Industry is all set to employ specialists in resource and process management rather than technology change in the manufacturing of textiles. The replacement of mechanical gadgets with electronic components in almost all types of machines has also given opportunities for specialists in PLC maintenance. The current trend of appointing these specialists shows that they will be working as freelance specialists rather than working as full time employees.
Major Challenges encountered:
Employment
Industry 4.0 compels the employees to develop altogether a new set of skills. This can cause alienation of big sector workers. Workers having a repetitive nature of work will face a challenge in keeping up with the industry. Older senior workers tend to find it difficult to undergo the learning process of new skills.
Capital
The investment in a new technology always requires a considerable amount of capital. A lot of planning and a good understanding of the industry requirements is of due importance. Smaller businesses might have to risk their market shares in the future. Considering all this, calculated risks are required to be taken.
Privacy
This not just a matter of concern for the consumers but also for the producers. The collection and analysing of data by the producers is taken to be a threat to the privacy of the consumers. Besides this, the smaller companies that have never handled data are exposed to a transparent environment in no time.
Some others to mention would be recruiting and developing new talent, conducting successful pilots, thorough examination of company culture and genuine interconnections of all the departments.
Success and Progress from Industry 4.0 to Industry 5.0:
The Textile Industry 4.0 has developed approaches to enhance contribution of manufacturing to GDP from 16% to 25%. Time and cost reduction to market by 50% was aimed. Value addition enhancement by 10% per year and slash rejection rate by 50% is being worked on. A three-year plan was proposed and is in process in order to become the globally networked enterprise. Various environment friendly approaches in manufacturing have been considered. For example, reduction of energy used (upto 30%), reduced waste water generation (upto 20% ), Less consumption of materials (upto 20%).
The Textile Industry 4.0 has made a significant social impact as well. It aims at creating sustainable care and responsibility for employees and citizens in the global supply chains. Its prime aim has also resided in raising investment and R&D from 0.5 to 4%.
Nevertheless, the visionaries have already predicted the next revolution, being just half a decade after the implementation of the current revolution. Industry 5.0 will see man and machine reconcile for improving the means and efficiency of production. It will witness the interaction of human intelligence and cognitive computing. The revolution will have the biggest advantage of being highly environmental friendly owing to the use of renewable sources of energy and eliminated waste.
Benefits of Adopting an Industry
4.0 Model
Industry 4.0 spans the entire
product life cycle and supply chain— design, sales, inventory, scheduling,
quality, engineering, and customer and field service. Everyone shares informed,
up-to-date, relevant views of production and business processes—and much richer
and more timely analytics.
Here is a quick, non-exhaustive
list of some of the benefits of adopting an Industry 4.0 model for your business:
It makes you more competitive, especially against disruptors like
Amazon. As companies like Amazon continue to optimize logistics and supply
chain management, you need to be investing in technology and solutions that
help you improve and optimize your own operation. To stay competitive, you have
to have the systems and processes in place to allow you to provide the same
level of service (or better) to your customers and clients that they could be
getting from a company like Amazon.
It makes you more attractive to the younger workforce. Companies that
invest in modern, innovative Industry 4.0 technologies are better positioned to
attract and retain new workers.
It makes your team stronger and more collaborative. Companies that
invest in Industry 4.0 solutions can increase efficiency, boost collaboration
between departments, enable predictive and prescriptive analytics, and allow
people including operators, managers, and executives to more fully leverage
real-time data and intelligence to make better decisions while managing their
day-to-day responsibilities.
It allows you to address potential issues before they become big
problems. Predictive analytics, real-time data, internet-connected machinery,
and automation can all help you be more proactive when it comes to addressing
and solving potential maintenance and supply chain management issues.
It allows you to trim costs, boost profits, and fuel growth. Industry
4.0 technology helps you manage and optimize all aspects of your manufacturing
processes and supply chain. It gives you access to the real-time data and
insights you need to make smarter, faster decisions about your business, which
can ultimately boost the efficiency and profitability of your entire operation.
5 Reasons Why Indusrty40 is a Game
Changer
1. Data can alleviate current
challenges for manufacturers.
2. It generates an innovation
economy.
3. The consumer become the central
focus
4. Workers become coordinators
instead of manual laborers
5. A sustainable prosperity
for business is on the cards.
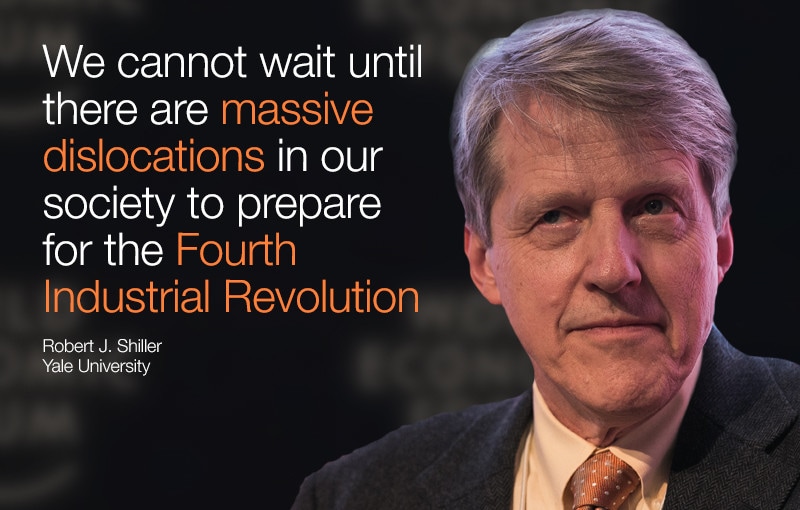
This is amazing. I liked it and you are doing a great job.
ReplyDeleteWe at UsedRobotsTrade, buy and sell used robots from a few designated robotics industries such as KUKA, ABB, MOTOMAN and others. Our KUKA used robot can be a good choice as it is well maintained and has high power and efficacy to do any job.