HUMIDIFICATION IN SPINNING MILLS
Air conditioning in spinning of fiber has many benefit, that
enhance profitability of process & product. Properties like dimensions, tensile strength,
elastic recovery, electrical resistance, rigidity etc. of all textile fiber
whether natural or synthetic are influenced by moisture regain, which
controlled by conditioning of air in mill.
There are not many occasions where humidity is more of an issue than during the processing of textile. Get it wrong and it can stop productions, damage machinery and harm staff. Get it right and you can maximize product weights, improve quality and increase machine speeds. The automatic air conditioning system used today is user friendly as well as efficient. Due to this proper and unique control on process without any interruption of humans. there fore newly developing mill gives prominence to automatic air conditioning plant. Last few years many conditioning companies developing new technologies and system for textile industries.
Air humidity is measured as “relative humidity”. It is defined as the amount of water in a sample of air compared to the maximum amount of water the air can hold at the same specific temperature. It’s expressed in a form of 0 to 100%.
Cold air can hold less moisture than warm air therefore the humidity of air is “relative” to its temperature. For example, a sample of air at 10oC can hold less moisture than the same sample of air at 20oC. Even with the same amount of water present in both samples, the warmer sample has a lower relative humidity as it can potentially hold more moisture than the cold air sample.
This means that even in humid climates, the indoor air humidity can be low when cool humid air from outside enters a textile production facility and its temperature rises. An increase in temperature of 20oC can lead to a typical drop in humidity of around 60%rH (relative humidity). This means that humid air entering a building at 80%rH would decrease to just 20%rH when heated. This can cause major problems for textile production.
All textiles are hygroscopic. That is, they absorb or release moisture depending on the relative humidity of the surrounding air. If the atmosphere is drier than the textile’s equilibrium relative humidity then the textile will give up its moisture to the air. If the air is very humid then the textile’s moisture content will increase. This moisture loss and gain occurs at every stage from the initial processing of the fibres through to final garment manufacturing, distribution and use by the consumer.
This change in moisture content has a direct impact on the properties of textiles, such as tensile strength, elasticity, fibre diameter and friction. A drop in the equilibrium relative humidity of a textile may cause it to be weaker, thinner, less elastic and therefore more brittle. It will also have more imperfections. By maintaining the air humidity whilst processing the fibres, this loss in moisture to the atmosphere is minimised.
Moisture loss during processing cannot be
totally eliminated as the act of processing will increase the
temperature of the material, which will cause it to become drier.
However, by increasing the humidity of the air surrounding the textile
directly after processing, the material experiences “regain”. Moisture
is reabsorbed by the textile, thus improving the quality and performance
of the fabric.
This regain also has a direct impact on the weight of the textile. As textile yarns are sold by weight, if a drop in humidity leads to a 4% reduction in weight, this will require 4% more fibre to be included in the sale product. For a mill manufacturing 80 tonnes of textile per day, this can lead to a loss of 3,200kg of product per day due to incorrect humidity control.
Static
The occurrence of static can be a major problem when processing textiles and it is directly related to levels of relative humidity. The electrical sensitivity that determines whether static electrification will occur is dependent on the moisture content of the air and fibres. As the fibres lose moisture, they increase their electrical resistance. This means they can no longer easily dissipate the electrical charge which is generated by the frictional contact with the machinery.
In a textile production facility with a low humidity, static discharges can jump up to 4-5 inches and, although they have a low current, can build up to several hundred thousand volts. This presents a danger to staff working with the machines as it is not only very uncomfortable if they are shocked, but it can cause a person to jump and fall, which presents extreme risks when working near to textile machinery. The static discharge can also present a direct health risk to people with weak hearts or pace makers fitted.
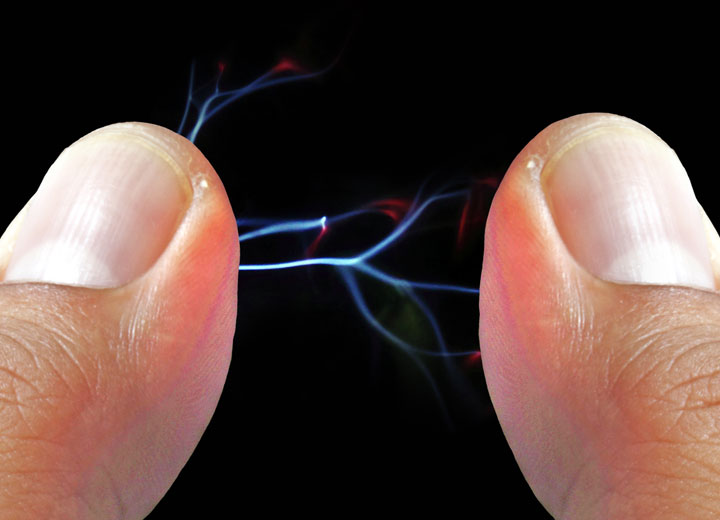
Humidity levels
IMPORTANCE OF RH AND TEMPERATURE:
The atmospheric conditions with respect to temperature and humidity play very important part in the
manufacutring process of textile yarns and fabrics.
The properties like dimensions, weight, tensile
strength, elastic recovery, electrical resistance, rigidity etc. of all textile fibre whether natural or
synthetic are influenced by Moisture Regain.
Moisture regain is the ratio of the moisture to the bone-dry weight of the material expressed as a
percentage.
Many properties of textile materials vary considerably with moisture regain, which in turn is affected
by the ambient Relative Humidity (RH) and Temparature. If a dry textile material is placed in a room with
a particualr set of ambient conditions, it absorbs moisture and in course of time, attains an equilibrium.
Some physical properties of textile materials which is affected by RH is given below:
of moisture the air will hold in suspension and , therefore, temperature and humidity must be considered together.
PSYCHROMETRY:
psychrometrics is the study of the thermodynamic properties of air and water vapour mixture or simply
the study of solubility of moisture in air at different temperatures , the associated heat contents
and the method of controlling the thermal properties of air. There are various properties of moist air, they are
This regain also has a direct impact on the weight of the textile. As textile yarns are sold by weight, if a drop in humidity leads to a 4% reduction in weight, this will require 4% more fibre to be included in the sale product. For a mill manufacturing 80 tonnes of textile per day, this can lead to a loss of 3,200kg of product per day due to incorrect humidity control.
Static
The occurrence of static can be a major problem when processing textiles and it is directly related to levels of relative humidity. The electrical sensitivity that determines whether static electrification will occur is dependent on the moisture content of the air and fibres. As the fibres lose moisture, they increase their electrical resistance. This means they can no longer easily dissipate the electrical charge which is generated by the frictional contact with the machinery.
In a textile production facility with a low humidity, static discharges can jump up to 4-5 inches and, although they have a low current, can build up to several hundred thousand volts. This presents a danger to staff working with the machines as it is not only very uncomfortable if they are shocked, but it can cause a person to jump and fall, which presents extreme risks when working near to textile machinery. The static discharge can also present a direct health risk to people with weak hearts or pace makers fitted.
As well as the physical danger to staff, static electrical build-up will cause materials to stick together and be less manageable. This in turn will slow machinery, directly effecting production schedules. Also, as most machines are now microprocessor controlled, an uncontrolled electrical discharge in the wrong place can damage the electronics of the unit resulting in expensive repair bills and significant downtime.
By maintaining humidity at around 50%rH, static build-up is eliminated and all these associated problems are avoided.
Another advantage of maintaining the correct humidity in processing facilities is that it reduces airborne particles. A higher humidity encourages airborne lint, dust and fly to precipitate out of the atmosphere. Also, if a cold water humidification system is used, the evaporation of the water into the air causes an adiabatic cooling effect that can reduce ambient temperatures by between 2-6oC. These additional benefits of using humidifiers create a healthier, less polluted, more pleasant atmosphere for workers and a more productive workforce.
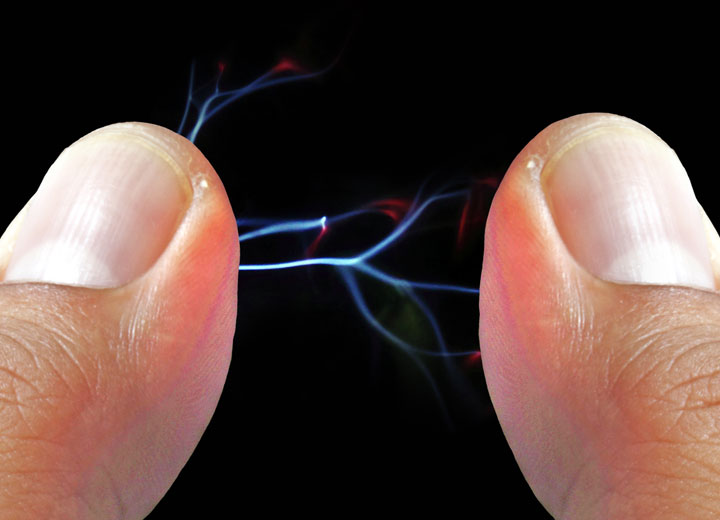
Hygiene
Hygiene is of paramount importance when releasing water into an atmosphere as any viruses or bacteria in the water could potentially be inhaled by people in the vicinity. Modern humidification systems incorporate a variety of hygiene features but the most effective type should combine both flush cycles and a form of silver ion dosing. The flush cycles will ensure that water cannot stagnate in the pipes and allow bacteria to form. Any cold water humidification system should typically auto-flush at least every 24 hours.
Silver ion dosing is a relatively new development in hygiene control in humidifiers. As silver is effective against over 650 types of bacteria and virus, it provides added reassurance by eliminating any organisms in the water before they enter the system. Silver also has a residual effect throughout the pipework. In the past humidifiers typically used to incorporate UV sterilisation but this can potentially allow viruses to enter the system “shadowed” by particles in the water, or allowed in by UV bulbs that have dulled with age.
Regular servicing is also an important aspect of hygienic humidification. No matter what hygiene features a system has, inspections should be carried out by a competent individual from time to time to ensure optimum and hygienic performance. Spray systems.
Humidity levels
So what is the ideal humidity? Well this depends on the type of textile and the process being undertaken. Natural fibres are far more susceptible to moisture than manmade, in terms of performance. However manmade textiles suffer more with static charge build up.
Cotton and linen have to be processed at very high levels, around 70-80%RH, because they are very brittle. By humidifying each process, from the combing of the raw material, through carding, twisting, spinning and weaving, the manufacturer can ensure that the product remains flexible and is prevented from breaking. This is important since the longer the fibre, the finer the thread that can be spun from it.
Wool is similarly susceptible to dry air, although a little more forgiving, requiring humidity levels of around 65%RH. Man-made fibres also require the correct, albeit lower, level of humidity since below 45%RH they are prone to a build-up of static electricity. Silk should be processed at between 65-70%RH, although artificial silk spinning requires a higher level of RH.
IMPORTANCE OF RH AND TEMPERATURE:
The atmospheric conditions with respect to temperature and humidity play very important part in the
manufacutring process of textile yarns and fabrics.
The properties like dimensions, weight, tensile
strength, elastic recovery, electrical resistance, rigidity etc. of all textile fibre whether natural or
synthetic are influenced by Moisture Regain.
Moisture regain is the ratio of the moisture to the bone-dry weight of the material expressed as a
percentage.
Many properties of textile materials vary considerably with moisture regain, which in turn is affected
by the ambient Relative Humidity (RH) and Temparature. If a dry textile material is placed in a room with
a particualr set of ambient conditions, it absorbs moisture and in course of time, attains an equilibrium.
Some physical properties of textile materials which is affected by RH is given below:
- Strength of COTTON goes up when R.H.% goes up
- Strength of VISCOSE goes down when R.H.% goes up
- Elongation %ge goes up with increased R.H.% for most textile fibres
- the tendency for generation of static electricity due to friction decreases as RH goes up
- At higher levels of RH , there is also a tendency of the fibres to stick together
of moisture the air will hold in suspension and , therefore, temperature and humidity must be considered together.
PSYCHROMETRY:
psychrometrics is the study of the thermodynamic properties of air and water vapour mixture or simply
the study of solubility of moisture in air at different temperatures , the associated heat contents
and the method of controlling the thermal properties of air. There are various properties of moist air, they are
- enthalpy etc.-
DRY BULB TEMPERATURE:
This is the temperature of air-moisture mixture as registered by an ordinary thermometer.
WET BULB TEMPERATURE:
It is the temperature of air-moisture mixture as registered by a thermometer where the Bulb is covered
with the wetted wick.
DEW POINT TEMPERATURE:
This is the temperature of air at which moisture starts condensing when air is cooled.
SPECIFIC HUMIDITY:
This is the weight of water vapour present in unit weight of dry air.
RELATIVE HUMIDITY:
This is the ratio of the mass of water vapour to the mass of dry air with which the water vapour is associated
to form the moist air. Relative humidity is a measure of how thirsty the air is at a given temparature.
At 100%, the air is completely saturated. At 50%, the air holds one-half of what it could hold if saturated
at the same temperature. The thirstier the air, the lower the percentage and the more it can rob fibres of moisture.
SPECIFIC VOLUME:
It is the volume per unit weight of air.
It is the total heat contained in unit weight of air, taking the heat content of dry air at 0 degree
centigrade. Enthalpy includes both the sensible heat and latent heat contained in the air.
SENSIBLE HEAT AND LATENT HEAT:
Sensible Heat is any heat that raises the temperature but not the moisture content of the substance.
This is our regular and familiar every day heat. Because it raises the temperature it can be detected by the senses, and this in fact, is why it is called Sensible Heat.
Latent Heat is the tricky one. When we talk of Latent Heat we mean 'Latent Heat of Vaporisation'.
It is that heat required to transform a liquid to vapour. Take water for example. Water can be
heated to its boiling point of 100oC. If more heat is added at this point the temperature of the
water does not increase. The water continues to boil and becomes steam. So where does all the heat go? Well, the heat goes into changing the water into steam. The latent heat of vaporisation in this instance is the heat required to change water from liquid at 100oC to vapour at the same temperature.
TYPICAL AIR-CONDITIONING PROCESSES:
SENSIBLE COOLING / HEATING:
Involving a sensible change in the temperature of air with the specific temperature of air with the specific humidity
or moisture content of air remaining the same. This process is shown as a horzontal line in Psychrometric chart
as no moisutre has been added or removed from the air and the humidity ratio remains the same.
The heat required to bring this change is shown below
H = G(h2-h1)
H = (Q/V)(h2-h1)
Where,
H is the rate of heat flow, kcal/h
G is the mass rate of flow of air, kg/h
Q is the volume rate of flow of air, meter cube / h
h1,h2 are the enthalpy before and after heating, kcal/kg
V is specific volume of air, meter cube/ kg
COOLING AND DEHUMIDIFICATION:
This is a process invoving reduction in both the dry bulb temperature and the specific humidity.
If air is cooled to temperature below its dewpoint, condensation of moisture occurs. This condensation
continues as long as the air is being further cooled. By noting the enthalpy of air before and after cooling,
we can determine the heat to be extracted or the tonnage of refrigeration required for cooling air continuously.
COOLING AND HUMDIFICATION:
This is a process involving reduction in DRY BULB Temperature and increase in specific humidity.
HEATING AND DEHUMIDIFICATION:
This is a process where there is an increase in DRY BULB temperature and reduction in speccific humidity.
LATENT HEATING:
This is a process where there is only an increase in specific humidity. This is a process of steam injection.
HEATING AND HUMIDIFICATION:
This is the process where there is an increase in both DRY BULB temperature and specific humidity.
EVAPORATIVE COOLING:
This is a process of cooling and humdification but with no change in the enthalpy of air during the process.
This is the process through an air-washer using recirculated water for spraying. This is the most commonly used humidification system in a textile mill.
-
ADIABATIC SATURATION OR EVAPORATIVE COOLING:
In this process air comes in direct contact with water in the air washer.There is heat and mass transfer
between air and water. The humidity ratio of air increases. If the time of contact is sufficient, the
air gets saturated. Latent heat of evaporation required for conversion of water into water vapor is taken from
the remaining water.When equilibrium conditions are reached, water cools down to the wet bulb temperature
of the air.In general it is assumed that, the wet bulb temperature and before and after the process is the same.
If the air washer is ideal, the dry bulb temperature and wet bulb temperature of the air would be eqaual.
If a process is adiabatic, heat is neither added or removed from the system
of some part of the water. That is why it is called EVAPORATIVE COOLING.
The sensible heat is decreased as the temperature goes down but the latent heat goes up as water vapour
is added to the air.The latent heat required by the water which is evaporated in the air is drawn from the
sensible heat of the same air.Thus it is transformation of sensible heat to latent heat. During this process
the enthalpy of air remains the same.
If humidity ratios of saturated air and of the air before saturation is known, then the difference between
the two would be the amount of water vapour absorbed by unit weight of dry air.
The amount of water sprayed in the air-washer to maintain misty condition can be as much as 200 times the
quantity of water absorbed by the air during summer time.
AIR CONDITIONING PROCESS FOR THE TEXTILE INDUSTRY:
Air is drawn in and is passed through the air washer, it gets saturated adiabatically. Since it is not
saturated 100%, the dry bulb temperature of the saturated air will be 1 degree greater than WBT.
When this air is admitted into the conditioned space, it gets heated due to the heat load of the room.
During this heating process the air does not lose or gain any moisture as latent heat load is absent.
The air displaces an equal amount of air in the room which is pushed outside the room.
If we know the heat load of the room, we can easily calculate the rate of flow of air, G, which is the air
circulation rate necessary to give the required relative humidity, from the following formula.
where,
G-mass flow rate of dry air, KG/h
H-total heat of air,Kcal/h
h1-enthalpy of supply air, Kcal/kg
h2-enthalpy of outgoing air,Kcal/kg
The air circulation rate is generally expressed in cubic meters per hour and not in terms of mass
flow rate. (h2-h1) can be calculated from the initial and final temperatures. Therefore
H = (Q/V)* Cp * (DB2-DB1)
Where,
Q-rate of air flow,metercube/h
Cp- specific heat of air
V-specific volume of air,metercube/kg
DB1- supply air DBT,degree centigrade
DB2- leaving air DBT,degree centigrade
However in practice, the air washer does not continuously supply air of 100% RH. The efficiency of air
washer falls. It is considered satisfactory, if the difference between DBT and WBT of air after the air washer is 1 degree centigrade.
The following equation can be used for practical purposes.
(DB2-DB1) = ((3.39 H)/Q)+0.52
Once the relative humidity to be maintained is decided, the quantity (DB2-DB1) is fixed. In other words,
once the inside relative humidity is fixed, the minimum dry bulb temperature in the condition space
is determined by the wet bulb temp. of the outside air. It is not possible to go below this DBT unless
refrigeration is used.
Why refrigeration is required?
Let us assume that WBT of outside temp is 35 degrees. If the RH% to be maintained in the department is 60%,
then DBT of the conditioned space should be 43.5 degrees. Whatever we do , we cannot reduce this temperature
as long as we are maintaining a RH OF 60%. Underthis circumstance, refrigeration plant is required to
bring down the WBT of the air inside, so that 60% RH can be maintained at lower DBT depending on
the refrigeration capacity.
HUMIDIFICATION SYSTEM:
Humidification system without chilling helps to maintain only the RH% without much difficulty. They can be classified generally as either unitary or central station. Central system is the most widely used sytem in the textile industry. The systems principal components are
- Air moving devices- fans
- mixing devices for air and washer- i.e Air washers
Air moving devices are always broken into two halves, 1. Return Air fans and 2.Supply Air fans.
The return air fans return the air to the plant room from where it may circulated or exhausted in the mill
The supply air fans- supply air to the mill from the plant room.
Air washer is a device for intimately mxing water and air. The intimate contact between these two elements is best brought about- for this application- by drawing air through a spray chamber in which atomized water is kept in transit.
The following components are a must in a Humidification system
- Return Air and Supply Air fans
- Air washer
- Return Air floor grills
- Return Air trenches
- Exhaust damper
- Fresh air damper
- Supply air ducts and grills
- face and bypass dampers on the air washer
- Automation control for damper operation to maintain conditions
-
ADIABATIC SATURATION OR EVAPORATIVE COOLING:
- Dry bulb temperature
- wet bulb temperature
- dew point temperature
- relative humidity
- specific voulme
-
FANS:
In any air handling system the fan is a key conponent. It is a device which moves the air. This is achieved
by pressurising the air, the resultant pressure difference makes the air to move. Fans can be classifed as follows
- Classification by air movement-1. centrifugal fan 2. Axial flow fan
- Classification by housing design -1. Scroll fans 2. Tubular fans
- Classification by pressure range- 1. high pressure 2. medium pressure and 3. low pressure
- Classification by Blade configuration - 1.forward curved blades 2.backward curved blades
From the fan laws the following relationship can be arrived
- CFM is directly proportional to fan RPM
- Pressure is directly proportional to sqaure of RPM
- Shaft power is directly proportional to cube of RPM
AIR WASHER:
Basic factors that determine the size of air washer are
- Velocity of air through the washer
- Type of nozzle used
- Water quantity in circulation
- No.of spray banks
The main components in an Air washer are
- Distribution plates
- Distribution Louvers
- Water pipes
- discharge headers
- stand pipes
- nozzles
- Eliminators
REFRIGERATION:
Air conditioning is a process to remove the heat from the place to be conditioned and reject the heat to
a place where it is not objectionable. In other words, a heat pump is required to accomplish the same. The
heat pump is called the refrigeration machine.
There are three types of refrigeration machines classified according to their type of operation. They are
- vapour compression system
- absorption system
- vacuum
- compressor
- condenser
- metering device
- evaporator
- operating controls
- safety controls
- accessories
- THE COMPRESSOR:
Under atmospheric temperature and pressure the refrigerant is in gaseous form. It is true that
the cooling takes place when liquids evaporate to become gas. Therefore the gas refrigerant must be transformed
into the liquid form. Most gasses can be made into the liquid form by raising its pressure (and cooling it,
which is handled by the condenser). The equipment that increases the pressure of the gas by compressing it,
is called the Compressor. Different types of compressors are
1.Reciprocating 2.Centrifugal 3.Rotary and 4.screw
THE CONDENSER:
During compression however the refrigerant becomes hot. This is because of two reasons:
- Because of the work done on it (remember how warm the hand pump became when pumping air into your bicycle tires?) and
- Because the refrigerant is converted from gas to liquid releasing its latent heat
the heat is called the Condenser. Different types are
1.Air cooled 2.water cooled and 3.evaporative condenser
EVAPORATOR:
The Evaporator ('Cooling Coil' to most of us): From the condenser we now have the liquid refrigerant ready to go to work. This refrigerant can remove heat when it starts evaporating. The liquid refrigerant from the condenser is injected through a metering device called the capillary or expansion valve into the cooling coil which is a bundle of tubes.
Inside the cooling coil the pressure is low, because of the metering/throttling device on one side and the compressor suction on the other side. In the low pressure, the liquid refrigerant Starts evaporating rapidly. While evaporating it needs sensible heat to transform itself from the liquid to the gas state. So it soaks up heat from the surrounding tubes, and from the air, with which the tubes are in contact. This is what causes the cooling.
Atmospheric Conditions and Relative Humidity:The dampness of the atmosphere can be calculated in terms of humidityAbsolute humidity:The weight of water present in a unit volume of moist air, i.e. grams/m3Relative Humidity: The ratio of the absolute humidity of the air to that of air saturated with water vapour at the same temperature and pressure, expressed as a percentage.Std. Testing Atmosphere:R. H. % : 65% ± 2%
Temp.: 20o C ± 2o C (cold countries)27o C ± 2o C (tropical & subtropical countries)Measurement of R. H. %:Hygrometer – Wet and Dry bulb hygrometer Dry bulb reading – 68o F Wet bulb reading – 61o F Difference – 7o F R. H. % from table 67 %
Generally the roof heating by solar radiation causes 50 %of the heat load in any premises. Hence attic Ventilation is low cost & preventive compared to high cost of cooling of
equipments & premises under attic.
In the Exhaust fans of AC plants, Pressure die casted blades of weight 15 kgs instead of the existing gravity casted blades of weight 35 KGs in the Exhaust fans will bring down the power consumptionby20 without Compromising static pressure across the air system and maintaining the same flow rates inside the premises.
Some of the mills do cost cutting by not running exhaust fans. This is not healthy sign of working.If at all you want to save power, clean the air filters in the return air exhaust frequently & reduce restrictions in line.
Spinning of yarn from cotton and then weaving or knitting cloth from the yarn is known to mankind millennium. It is probably one of the first crafts developed as men’s thought of civilization, the ancient learnt that if water is sprayed on the floor in hot days or if we get wet cloth is kept over yarn , working is easier because of less yarn breakages. This was state of affairs till 200 years back, but as industrial revolution takes place mass production was aimed, different methods were developed to provide moisture to material to the material in process. As the machine heat added it create problem to RH%. In olden days people are using water cans and more number of windows which may not suitable for high speed.
![]() |
Image: Air conditioned spinning mill |
NEED OF RH% CONTROL IN SPINNING:
Correct ambient conditions are essential to prevent degradation of textile material during a series of operation right from beating in blow room to weaving. Yarn should have requisite properties so that the final product retains its basic shape, size & strength.
(When Humidity is High):- Fiber tends to stick and lead to formation of laps on rolls which disrupt production process. Removal of laps is not only a manual and time consuming process, but result in damage of machine part , especially the rubber material (apron, top roller etc.).
(When Humidity Is Low ):- Fiber become brittle and store electric charges generated because of friction between the fiber during their spinning process, which affect fiber properties and machine too.
In modern spinning machine designed with high speed which increase in temperature of mill and affect process. Whereas , modern machine has electronic control panel which requires specific temperature. Textile machinery generally are made of steel and aluminum which shows expansion during process with different rate which generate thermal and mechanical stress in machines.
Hence along with maintenance of stable RH% condition, recommended for textile and also to maintain the temperature level within range.
GENERAL REASONS FOR RH% AND TEMPERATURE CONTROL:-
- Dry air causes low regain, yarn with low moisture content are weaker thinner, more brittle & less elastic and prone to generate static charge.
- Material at optimum regain has controlled properties, lower imperfections, more uniform yarn.
- Higher humidity reduces static problems and machine can run at higher speed.
- Textile weight are standardized at 60% RH and 20degree C , low humidity causes lower material weight and less profit.
- Humidification reduces fly and micro dust, giving a healthier and more comfortable working environment
![]() |
Image: General recommendations of RH% for spinning |
![]() |
Image: General recommendations of temperatures for spinning |
The rotor spinning system
imposes no special conditions and requirements on its environment; i.e.
the customary ambient conditions in a spinning mill as regards
temperature, humidity and air conditioning are always adequate for rotor
spinning, and in many cases are even less critical than for ring
spinning. Only relative humidity levels are slightly higher than for
ring spinning.
Raw materials behave differently not only as regards
their readiness to absorb moisture, their running properties are also
affected by humidity levels in the spinning mill. Since the raw material
spends several days in the spinning mill on its way through the
spinning process, the moisture content of the fibers depends on the
moisture content of the ambient air. Absolute moisture content in g/kg
air therefore plays a crucial role in a favorable spinning climate. This
moisture content is created by a combination of air temperature (°C or
°F) and relative humidity (RH%). Table shows the required absolute
moisture content in g/kg air for a favorable spinning climate.
The more precisely the standard climate, i.e. relative
humidity, is maintained within limits, the more trouble-free spinning
operations are. While cotton and viscose react somewhat less
problematically to changes in the ambient climate, changes soon become
obviously apparent when man-made fibers are being processed.
If relative humidity is too low, this usually becomes
apparent with man-made fibers in electrostatic charging and a consequent
increase in ends down. When cotton is being processed, fiber damage,
fiber fly and deposits in the spinning box and winding zones occur.
If relative humidity is too high, this results in
lapping on cylinders and opening rollers with all fibers. The spin
finish on man-made fibers tends to leave deposits on thread guide
elements and in the fiber guide channel, thus obstructing fiber
transport to the rotor. This then results in an increase in the number
of neps and thick places.
There are many different issues involved with humidification of textile plant and as above described in discussions, getting it wrong can be an expensive mistake. So to control process, production, quality, comfort conditioning of air is necessary, even though humidification plant consumes 15% of energy of total spinning plant. That 15% cost can be overcome by improving quality and production of yarn. In proper conditioning, it is to work and control the production. As above mentioned condition of RH% and temperatures for that specific process gives good efficiency and less machine maintenance.
An overview of the advantages of using air humidification in the textile industry:
- Reduces production downtime
- Increases productivity and product quality
- Protects against dangerous electrostatic discharge
- Creates a healthy and pleasant working environment for operational staff
Automation And Digitization
New plants are fully automated and no manual interventions/adjustments are required. Earlier, it was needed to adjust the dampers and water pump flow to achieve required conditions inside. In modern humidification plants, all the fans and pumps are inverter controlled. High quality sensors give signals to damper /pump motors to adjust air quality going inside.
In modern humidification plants, likely, all the new features shall be available soon where one can access real time data anywhere from mobiles etc. All the data can be displayed inside the working areas also.
Better And Advance Software
The new software is much faster and quick to react to abrupt changes in the outside conditions. Accuracy has also improved with reliability of the system. There is no problems of system hanging and every time to restart it. One can see now latent heat data also on the screen along with grains/volume of air.
Energy Efficient
New fan design is supposed to give better efficiency and hence consumes less energy. Design of the complete plant has improved. Mechanical accuracy also
contributes to lower power consumption. Nowadays with pre-fabricated buildings , humidification plants can be mostly installed on ground floor with very less civil work barring water tanks etc
No comments:
Post a Comment