BAMBOO FIBRE - YARN - FABRIC
Bamboo textile fibre is made from bamboo timber which has matured in the forest for at least 4 years.
Bamboo botanically categorized as a grass and not a tree, bamboo just might be the world’s most sustainable resource. It is the fastest growing grass and can shoot up a yard or more a day. The first patents for bamboo paper occurred in 1864 and 1869.Mordern bamboo clothing was first introduced by Beijing University but commercial use increased during 2004-2010.
Even in remote areas of China and India bamboo forests are highly valued and carefully tended and managed. In summer, when new shoots reach their full height, they are marked with a year code which makes sure they are harvested at the right maturity. When harvested they are taken to mills where they are crushed and submersed in a strong solution of sodium hydroxide which dissolves the bamboo cellulose. With the addition of carbon disulfide it renders the mix ready to regenerate fibres which are then drawn off, washed and bleached to a bright white colour and dried. The resultant fluff is very long in staple and visibly finer than other fibres. Then they are spun into yarn, like any other textile fibre. The longer staple and higher tensile strength is what makes a tough, soft yarn – which is not as susceptible to wearing and fraying as many other yarns. This is what gives bamboo fabrics excellent durability. The hollowness of the fibre contributes to its very high level of absorbency. But it also takes longer to dry on a clothesline. The hollowness of the fibre also enables it to hold dyes and pigments more readily and permanently, thus making it much more colourfast.
The two main chemicals used in the process are sodium hydroxide and carbon disufide.
It was only discovered that carbon disulfide was a nerve poison after many years of exposure at high concentrations by factory workers in Italy in the 1930s and 40s. With adequate ventilation it is not a problem these days and it breaks down when in contact with the natural elements. Neither carbon nor sulfur are poisonous elements.
Sodium hydroxide is also known as caustic soda, and it is true that it is strongly alkaline and will react with many substances. However, it is not toxic at all and is used extensively in cooking. Used in quite high concentrations it is what gives traditional pretzels their distinctive flavour.
Bamboo leaves and the soft, inner pith from the hard bamboo trunk are extracted and crushed.The crushed bamboo cellulose is soaked in a solution of 15% to 20% sodium hydroxide at a temperature between 20 degrees C to 25 degrees C for one to three hours to form alkali cellulose. The bamboo alkali cellulose is then pressed to remove any excess sodium hydroxide solution. The alkali cellulose is crashed by a grinder and left to dry for 24 hours. Roughly a third as much carbon disulfide is added to the bamboo alkali cellulose to sulfurize the compound causing it to jell. Any remaining carbon disulfide is removed by evaporation due to decompression and cellulose sodium xanthogenate is the result.A diluted solution of sodium hydroxide is added to the cellulose sodium xanthogenate dissolving it to create a viscose solution consisting of about 5% sodium hydroxide and 7% to 15% bamboo fiber cellulose. The viscose bamboo cellulose is forced through spinneret nozzles into a large container of a diluted sulfuric acid solution which hardens the viscose bamboo cellulose sodium xanthogenate and reconverts it to cellulose bamboo fiber threads which are spun into bamboo fiber yarns to be woven into reconstructed and regenerated bamboo fabric. Newer manufacturing facilities have begun using other technologies to chemically manufacture bamboo fiber that are more benign and eco-friendly. The chemical manufacturing process used to produce lyocell from wood cellulose can be modified to use bamboo cellulose. The lyocell process, also used to manufacture TENCEL®, uses N-methylmorpholine-N-oxide which is non-toxic to humans and the chemical manufacturing processes are closed-loop so 99.5% of the chemicals used during the processing are captured and recycled to be used again. Nano Technology is being also used for Bamboo fibers.
Mechanical Processing
During the mechanical processing of bamboo, the bamboo plant is crushed into a pulp. The bamboo’s natural enzymes are used to form a mushy substance from which fibers can be combed out. These fibers can then be spun into yarn, which is then used as bamboo fabric or linen to make cloth products. The mechanical processing of bamboo fiber is very eco-friendly, and is similar to the manufacturing of flax or hemp cloth.
Chemical Processing
Chemical processing is the most common form of bamboo fiber processing. Though many chemical processing methods are not environmentally friendly, there are some methods that are more eco friendly than others. Chemical processing of bamboo fibers involves “cooking” the fiber using chemicals to create a kind of regenerated cellulose fiber, which can then be used for thread and woven into cloth fabric. All parts of the bamboo plant are used in the process of turning it into usable fabric.
Environmentally Friendly Chemical Processing
The Lyocell process is generally considered to be the most environmentally friendly method of manufacturing bamboo cloth fiber. This is because it is in general more sustainable than most common chemical processing methods. According to the FTC, Lyocell is defined as a cellulose fabric made by an organic solvent spinning process. The chemicals used in this processing method are non-toxic and much safer for humans than other traditional processing chemicals. About 99.5% of the chemicals used are captured in a close-loop container, which means they can then be recycled with minimal amounts of them being released into the environment, avoiding air and water pollution.
Right now, people are still in the process of the developing new manufacturing methods to add to the available “green” options of bamboo fabric making. One of these processing methods is Greenyarn, which makes use of chemicals to form nano bamboo charcoal particles that can be woven into fabrics.
Common Chemical Processing Method
The most common chemical method of bamboo fabric manufacturing involve the use of carbon disulfide. First, the bamboo is crushed and its moisture kept at about 65%. The substance is then sulfirized by the addition of the carbon disulfide chemical. This step turns the bamboo cellulose solution into gel, which is in turn diluted using sodium hydroxide. The ensuing product is a viscous solution that gets passed through various nozzles and then place into another chemical solution and left to harden. After it has hardened, it gets converted into thread and spun into actual, usable fabric.
Regardless of how it is processed, bamboo makes for a very versatile clothing material. It has antibacterial qualities, for one, which it retains even after multiple washings. This means that bacteria that tend to thrive in clothing and cause unpleasant odors tend to not be as present in bamboo fabric. Bamboo can even kill odor causing bacteria in the wearer’s skin. It also has insulating qualities that help keep you warm in winter and cool in the summer.
The cellulase treatment harms the excellent functions of the bamboo fiber. Also, the product is expensive because mass production is very hard.
The present invention aims to solve such problems.
Solution to Problem
A method according to the present invention is for manufacturing blend yarn with bamboo fiber. The method includes: immersing bamboo in alkali solution; drying the bamboo took out from the alkali solution; obtaining bamboo fiber from the dried bamboo; performing a heat and pressure treatment over the obtained bamboo fiber; and mixing and spinning the treated bamboo fiber with second fiber to form blend yarn.The term “bamboo” is intended to mean any plants belonging to Bambusoideae. It may include Bambuseae, Arundinarieae, Olyreae and the like. Phyllostachys bambusoides, Phyllostachys nigra, Phyllostachys edulis, Neosinocalamus affinis, or the like is preferable because they have high toughness and flexibility. Also, the bamboo is preferable within the first year of growing, i.e., logged before 12 months pass after a bamboo shoot becomes bamboo. More preferably, the age of the bamboo is between 2 and 7 months, because it has excellent fiber strength and easy processing. Also, this enables to log new bamboos every year in order to manufacture bamboo fiber.
Before the immersing, bamboo joints may be eliminated from the bamboo. Removal of the bamboo joints, which are very hard, makes it easier to get the bamboo fiber from the bamboo.
Preferably, bamboo surfaces are not eliminated from the bamboo. Residual bamboo fibers derived from the bamboo surfaces, which causes high antibacterial, increases antibacterial of the blend yarn.
Bamboo may be cut to a predetermined length. This increases uniformity of lengths of the bamboo fibers.
The alkali solution is liquid with a pH over 7. It may include sodium hydroxide aqueous solution, ammonia water, sodium bicarbonate liquid, and the like. Immersing the bamboo in the alkali solution makes binder materials, such as lignin, dissolved. This facilitates obtaining the bamboo fiber from the bamboo. Also, this softens the bamboo fiber, especially derived from the bamboo surface.
Preferably, pH of the alkali solution is 10 or more. higher pH promotes more dissolution of the binder. In the case of sodium hydroxide aqueous solution, its concentration is preferably over 1 weight %.
However, too high pH causes damage of the bamboo fiber. Thus, the pH of the alkali solution is preferably 12 or less, and more preferably 11 or less. In the case of sodium hydroxide aqueous solution, its concentration is preferably under 6 weight %, and more preferably under 3 weight %.
The immersing is performed for a sufficient period to make the alkali solution to soak into the bamboo and to dissolve the binder. A preferable duration depends on a thickness of the bamboo. Generally, it may be between 24 and 48 hours, or substantially 36 hours.
Preferably, the bamboo is not washed after took out from the alkali solution. This eliminates problems of industrial effluent polluted with the alkali solution.
The obtaining of the bamboo fiber is performed by dividing the bamboo into the bamboo fibers. The bamboo may be recarded using a recarding machine, and/or defibrated using a defibrating machine.
The heat and pressure treatment is for applying high temperature and high pressure objects, i.e., bamboo fiber. It may include dry distillation treatment, steam explosion treatment, and the like. This removes impurities, such as oil, water, worms, and the like. Residue of the alkali solution, such as sodium hydroxide, is also removed. Lignin is changed to polyphenol, which strengthens antioxidative effect. Also, increasing porosity notably reinforces adsorption of odor, adhesion of floating materials such as formaldehyde or the like, antifungal effect, and the like. Also, combining the heat and pressure treatment with the immersing treatment makes the bamboo fiber, especially derived from the bamboo surface, further soft to restrain prickle sensation.
The dry distillation treatment is for heating objects inside a hermetic vessel such as a pot. This causes pyrolysis without combustion.
The steam explosion treatment is for holding objects under hyperbaric environment, and then suddenly reducing the pressure. This causes breaking the objects in pieces.
Preferable maximum pressure achieved in the heat and pressure treatment is between 5 and 6 atmospheric pressures, i.e., more than about 5,000 hPa (hectopascal) and less than about 6,000 hPa.
Preferable maximum temperature achieved in the heat and pressure treatment is between 140 and 200° C., and more preferable is between 150 and 160° C.
Preferable duration of keeping the maximum pressure and the maximum temperature is between 3 and 10 minutes.
Before the mixing and spinning, the bamboo fiber may be preprocessed, such as screening, drying, or the like. For example, bamboo fibers with lengths between about 15 and about 70 mm and average diameters of 0.2 mm or smaller, preferably between about 0.07 and about 0.1 mm, are extracted from the obtained bamboo fibers. longer and/or thicker bamboo fiber causes higher content rate in the blend yarn, which enhances functions derived from bamboo. Uniformity of lengths and/or thickness of the bamboo fibers promotes entanglement with the second fibers, which facilitates the mixing and spinning. Almost the same lengths of the bamboo fiber as that of the second fiber enables uniform mixing and spinning.
The second fiber may be any fiber except bamboo fiber. It may be derived from plant such as cotton or flax, animal such as sheep or silkworm, or any other sources. Also, it may be natural fiber such as cotton or silk, or artificial fiber such as nylon or carbon fiber.
Before the mixing and spinning, the second fiber may be preprocessed, such as mixing and blowing, cutting, or the like. For example, the second fibers may be cut to have about 40 mm lengths.
The bamboo fiber and the second fiber preferably have almost the same lengths. This enables uniform mixing and spinning
The mixing and spinning may include a mixing step, a carding step, a drawing step, a roving step, a fine spinning step, a winding step, and the like.
The mixing, or blending, step is for mixing the bamboo fiber and the second fiber. Changing a mixing ratio of the bamboo fiber to the second fiber enables the blend yarn to have various properties.
The carding step is for combing the fiber to form a sliver. This enables to uniform directions of the fibers, to remove dust, short fibers, and the like.
The drawing step is for drawing the slivers to form a drawn sliver. This produces uniformity of thickness of the slivers, and removal of short fibers. The drawing step may be performed repeatedly, i.e., applied to the drawn slivers.
The roving step is for drafting and twisting the sliver such as the drawn sliver, to form rove. This reduces the thickness of the sliver.
The fine spinning step is for further drafting and twisting the sliver or rove, to form yarn.
The winding step is for rewinding the yarn to form a large package. This enables to remove neps, dust, yarn unevenness, or the like.
Advantageous Effects of Invention
The present invention enables to manufacture blend yarn with bamboo fiber with low-cost, while keeping the excellent properties of the bamboo fiber. Products using the blend yarn inherits excellent functions from bamboo, such as high strength, antibacterial effect, antioxidative effect, deodorant effect, and soundproof effect, with no problems of texture and dyeability.BRIEF DESCRIPTION OF DRAWINGS
Referring to the accompanying drawings, embodiments will be described in detail. the embodiments and the drawings are provided only for more complete understanding of the present invention. They are not intended to limit the present invention in any meanings.Manufacturing Bamboo fiber
As shown in FIG. 1, Bamboo is firstly provided, for example, by logging bamboo within the first year of growing. And, bamboo splitting machine is used to split the provided bamboo into 4 to 6 pieces. Then, bamboo joints are eliminated from the split bamboo pieces. It should be noted that bamboo surfaces are not eliminated, in contrast to conventional methods. This enables blend yarn to inherit excellent properties, such as antibacterial, from the bamboo surface.
Next, the bamboo pieces are immersed in 1 to 6%, preferably 1 to 3%, sodium hydroxide aqueous solution. They are left as they are for about 36 hours.
Then, the bamboo pieces are took out from the solution. And, the bamboo pieces are drained and dried.
Next, bamboo fibers are obtained from the dried bamboo pieces. In some embodiments, a recarding machine may be used to scrape the bamboo pieces to make small fibers. Alternatively or Additionally, a pair or pairs of rollers may be used to crush the bamboo pieces to make them thinner, and a defibrating machine may be used to defibrate the crushed thin bamboo pieces to get fine and long fibers. In the same manner as strip processing of metal plates, each of the pairs of the rollers may be spaced with a different gap width, and they may be arranged in descending order of the gap widths. The rollers may have grooves with different shapes.
Then, the obtained bamboo fibers are screened to uniform their lengths and thickness. In some embodiments, the screening may be performed by eliminating nonstandard bamboo fibers, such as with lengths under 15 mm, with lengths over 70 mm, with average diameters under 0.07 mm, and with average diameters over 0.1 mm. The remaining bamboo fiber may further be dried.
Finally, dry distillation treatment is applied to the bamboo fibers. The dry distillation may be performed under 5.5 atmospheric pressures and 156° C. Alternatively, steam explosion treatment may be applied to the bamboo fibers.
Manufacturing Blend Yarn
As cotton fibers are firstly provided, as well as the manufactured bamboo fiber. The cotton fibers may have lengths of about 40 mm. Alternatively, silk fiber may be provided. The silk fiber may be cut to have about 40 mm lengths.Next, a mixing and blowing machine is used to mixing and blowing the provided cotton fibers to form a lap , which has a sheet shape and which includes a large number of randomly entangled cotton fibers. This eliminates dust adhered with the cotton fibers. Different types of cotton fiber may be mixed. This restrains un uniformity of quality. The lap may be wound around a roller.
Then, the cotton fiber lap is mixed with the bamboo fibers to make mixed fiber. The blend ratio may be arbitrary. Proportion of the bamboo fibers over 50% facilitates to exert excellent effect of bamboo fiber. In contrast, lower ratio of the bamboo fiber makes the mixing and spinning easier. However, a ratio of the bamboo fiber is preferable to be a few % or more, in order to keep excellent properties derived from bamboo.
Next, a carding machine is used to comb the mixed fiber to form a sliver. This makes the mixed fiber separated to each of the fibers, and arranged parallel. Also, small dust and short fibers are removed. Remaining long fibers, which include a large number of bamboo fibers and cotton fibers are shaped into a thin sheet, which is converged to form a converged sheet with a triangle shape, which is further converged to form a sliver with a string shape.
A drawing machine is used to double 6 or 8 strings of the slivers and draft them to increase their lengths by 6 or 8 times, to form one drawn sliver with a string shape. This makes the fibers straight, and eliminates unevenness of thickness to make the drawn sliver uniform. Also, short fibers are removed. A plurality of the drawn sliver may be drawn to form one further drawn sliver. The drawing step may be repeated 2 times or more.
Then, a roving machine is used to draft and twist the drawn sliver to form a rove. This makes the rove sufficiently thin to make blend yarn. The rove may be wound around a bobbin.
Next, the rove is further drafted and twisted to form a blend yarn, which is an end product. The twist of the blend yarn may be between 150 and 3000 turns per meter. The blend yarn may be immersed in and thereby coated with paste of arum root. This significantly enhances its fineness, and it can be used for making beautiful fabric or knitting. The blend yarn may be wound around a bobbin.
Finally, plural strings of the blend yarn are wound together to make one large package. The package may be shaped into a cone.
The blend yarn manufactured in this manner has about twice the strength of yarn made of only cotton fiber. Also, it has an adsorbing effect of formaldehyde or the like, a deodorizing effect, a soundproof effect, and an antibacterial effect against Staphylococcus aureus or the like. These effects are remarkable, and scarcely decreased even when laundered. The blend yarn is suitable to be used in products, especially required to have antioxidative effect, antibacterial effect, and/or deodorizing effect.
When the blend ratio of the bamboo fiber to the cotton fiber is 55:45, the blend yarn is suitable to be used for business shirts or jeans. This can be achieved by using cotton fiber with cotton count of 12, i.e., about 50 tex. When the blend ratio is 30:70, it is suitable to be used for socks or towels. This can be achieved by cotton fiber having cotton count of 20, i.e., about 300 tex. Using cotton fiber with cotton count of 5, i.e., about 120 tex, enables to make blend yarn in which the bamboo fiber is more than the cotton fiber and which is suitable to be used for shop curtains or carpet rags.
The manufacturing method in this manner is suitable to mass production. Also, its environmental load is very small. Thus, the blend yarn can be manufactured with low-cost.
The above described embodiments are examples to make it easier to understand the present invention. The present invention is not limited to the example, and includes any modified, altered, added, or removed variations, without departing from the scope of the claims attached herewith. This can be easily understood by persons skill in the art.
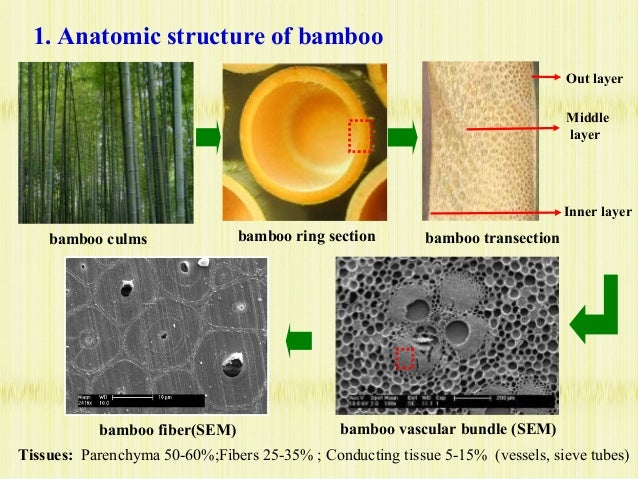
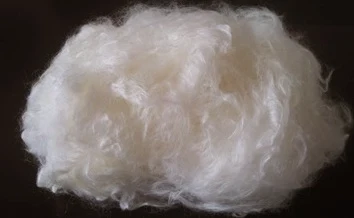
Bamboo fiber


Structure of bamboo fiber
Longitudinal View

Cross sectional View

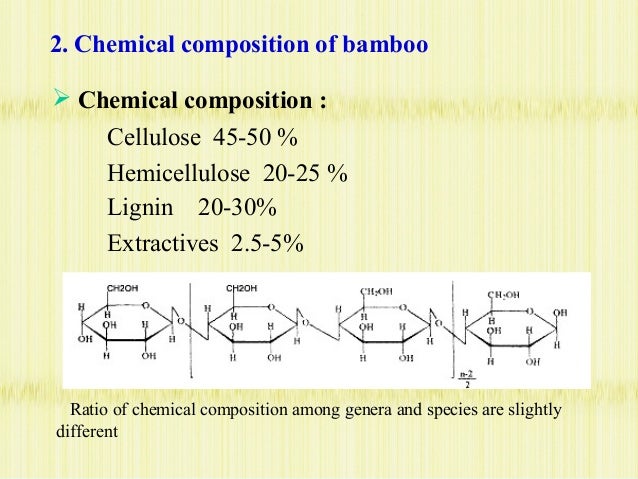
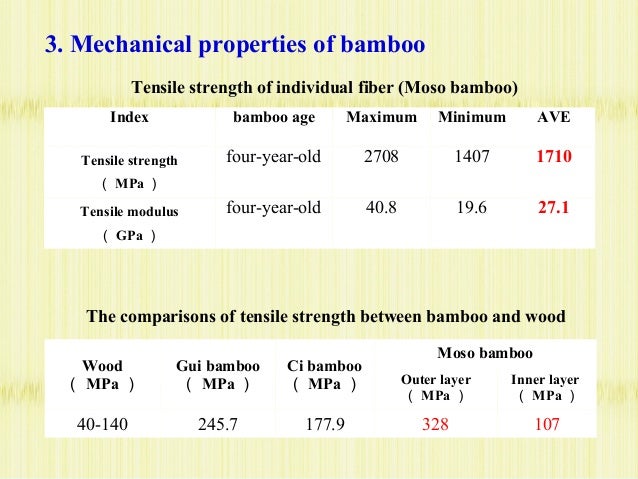
Characteristics of Bamboo Fiber
Bamboo fiber is naturally anti-bacterial, UV protective, green & biodegradable, breathable & cool, strong, flexible, soft and has a luxurious shiny appearance.
Smooth, Soft and Luxurious Feel: Bamboo fiber can be softer even than silk fiber when spun into yarn. It has a basic round surface which makes it very smooth and to sit perfectly next to the skin.
Good Absorption Ability: Bamboo fiber absorbs and evaporates sweat very quickly. It's ultimate breathability keeps the wearer comfortable and dry for a very longer period. It is 3-4 times more absorbent than cotton fabrics.
Temperature Adaptability: Fabrics made from bamboo fiber are highly breathable in hot weather and also keep the wearer warmer in cold season. Bamboo is naturally cool to the touch. The cross-section of the bamboo fiber is filled with various micro-gaps and micro-holes leading to much better moisture absorption and ventilation. It is also very warm in cold weather, because of the same micro structure as the warm air gets trapped next to the skin.
Antibacterial: Bamboo is naturally antibacterial, antifungal and anti-static. Bamboo has a unique anti-bacteria and bacteriostasis bio-agent named "bamboo kun" which bonds tightly with bamboo cellulose molecules during the normal process of bamboo fiber growth. This feature gets retained in bamboo fabrics too. Many tests have been conducted whose results show over 70% death rate after bacteria was incubated on bamboo fiber fabric. Tests by the Japanese Textile Inspection Association shows that, even after fifty washes, bamboo fabric still possessed these properties. It makes bamboo fabrics healthier, germ free and odor free.
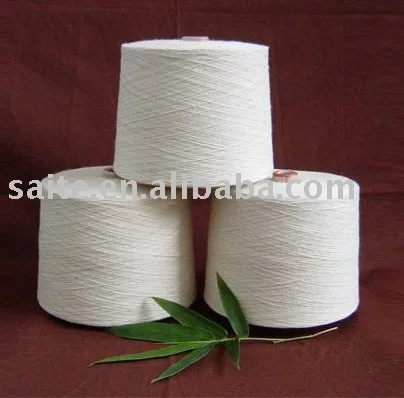
Bamboo knitting yarn is a relatively new entry in the knitting world, but it has become quite popular very quickly, and with good reason. Bamboo is a beautiful natural fiber that wears well and is often considered natural antibacterial.
Bamboo is a grass that is harvested and distilled into cellulose that is then spun into the yarn.
Positive Things About Bamboo Yarn
- Bamboo is a renewable resource. Bamboo can be harvested without killing the plant, and it only takes a few months before the plant is ready to be harvested again. That makes it an environmentally friendly choice
- Bamboo yarn, when not mixed with unnatural fibers, is biodegradable.
- Bamboo yarn is often dyed with more natural dyes that are safer for the environment.
- Bamboo fabric is naturally antibacterial.
- Bamboo also has ultra-violet protective properties.
- Fabric knitted with bamboo is quite breathable and cool and has great drape.
- Bamboo has a good luster, similar to mercerized cotton.
- Bamboo is strong, flexible, and can be softer than silk when spun into yarn.
Potential Bamboo Negatives
- Bamboo yarn loses strength when it is wet and swells considerably in water.
- The yarn may not be very cohesive. Some brands split much more than others.
- Bamboo needs to be hand-washed, so it isn't a great choice for things that need to be washed frequently.
Tips for Working with Bamboo Yarn
- If the antibacterial property is something you are looking for, stick with a 100 percent bamboo yarn or choose one that has at least 70 percent bamboo for best results.
- Use blunt-ended needles to cut down on the splitting (perhaps bamboo needles?).
- Knit slowly at first to avoid splitting.
- If you're looking for strength in the fabric but are using a fine bamboo yarn, try knitting with two strands held together.
- Bamboo fabric has a natural sheen and softness that feels and drapes like silk but is less expensive and more durable.
- Bamboo clothing is easy to launder in a clothes washer and dryer.
- Because of the smooth and round structure of its fibers, bamboo clothing is soft and non-irritating, even to sensitive skin. Some people with chemical sensitivities can not tolerate bamboo clothing. We are not sure if this intolerance is due to the intrinsic nature of bamboo but it more likely because of other chemicals added or used during the manufacturing and finishing processes of the clothing.
- Bamboo is naturally anti-bacterial and anti-fungal supposedly because of a bacteriostatis agent unique to bamboo plants called “bamboo kun” which also helps bamboo resist harboring odors. “Kun” is also sometimes spelled “kunh”. The bamboo kun in bamboo fabric stops odor-producing bacteria from growing and spreading in the bamboo cloth allowing bamboo clothing to be more hygienic and to remain fresher smelling.
- Bamboo clothing is hypoallergenic.
- Bamboo is highly absorbent and wicks water away from the body 3 to 4 times faster than cotton. In warm, humid and sweaty weather, bamboo clothing helps keep the wearer drier, cooler and more comfortable and doesn’t stick to the skin.
- The structure of bamboo fibers make bamboo fabrics more breathable and thermal regulating than cotton, hemp, wool or synthetic fabrics.
- Bamboo clothing is naturally more wrinkle-resistant than cotton, and while it might still require ironing after washing, bamboo fabric can be ironed at a lower temperature than cotton. Shrinkage during washing and drying is minimal at warm temperatures.
- Bamboo fibers and fabrics absorb dyes faster and more thoroughly than cotton, modal and viscose with better color clarity. Bamboo fabrics do not need to be mercerized to improve their luster and dye-ability like cotton requires.
- Disadvantages :
- Bamboo tends to shrink more than all
cotton fabrics, therefore special laundering may be required. Bamboo
fabric also wrinkles more than other fabrics. Depending on what the
fabric is being used for, bamboo may not be the ideal choice. sometimes
it is difficult to achieve antimicrobial finish.
The bottom line on bamboo.
The growing of bamboo is environmentally friendly but the manufacturing of bamboo into fabric raises environmental and health concerns because of the strong chemical solvents used to cook the bamboo plant into a viscose solution that is then reconstructed into cellulose fiber for weaving into yarn for fabric.
Bamboo clothing marketers have found a variety of ways to put the most eco-friendly and sustainable face on the manufacturing of bamboo fabric. The dominant manufacturing process of hydrolysis alkalization and multi-phase bleaching is generally referred to as a rather benign process utilizing caustic soda and bleach. The chemicals used are known to create a variety of health problems and neural disorders which can be hazardous to the health of fiber manufacturing workers. If the manufacturing facility lacks adequate pollution control systems – all too common in developing countries where regulations and enforcement are nearly non-existent – then these toxic chemicals can escape into the atmosphere through air vents and smokestacks and into waterways through inadequately treated waste water disposal systems.
Some bamboo fiber manufacturing facilities trumpet their sustainability and green credentials by establishing ISO 9000 Quality Management policies and ISO 14000 Environmental Management policies. This is largely a PR red herring tossed by the manufacturing facilities and marketers because these ISO standards do not mean that the facilities, their manufacturing processes or their fabrics have been certified by any of the international certification bodies such as SKAL, Soil Association, Demeter, KRAV, or OKOTex.
|
||||||||||||||||||||||||||||||||||||||||||||||||||||||||||||||||||||||||||||||||||||||||||||||||||||||||||||||||
Physical
Parameters of Bamboo Fiber
|
||||||||||||||||||||||||||||||||||||||||||||||||||||||||||||||||||||||||||||||||||||||||||||||||||||||||||||||||
Testing
condition: Temperature : 20 ℃ Relative humidity: 65%±3%)
|
1.5DX38MM
|
2DX51MM
|
3DX86MM
|
3DX89MM
|
3DX102MM
|
|||||||||||||||||||||||||||||||||||||||||||||||||||||||||||||||||||||||||||||||||||||||||||||||||||||||||||
Dry
tensile strength (CN/dtex)
|
2.15
|
2.11
|
2.4
|
2.36
|
2.29
|
|||||||||||||||||||||||||||||||||||||||||||||||||||||||||||||||||||||||||||||||||||||||||||||||||||||||||||
Dry
elongation at break (%)
|
24.9
|
25.7
|
21.2
|
19
|
18.1
|
|||||||||||||||||||||||||||||||||||||||||||||||||||||||||||||||||||||||||||||||||||||||||||||||||||||||||||
Wet
tensile strength (CN/dtex)
|
1.21
|
1.25
|
1.36
|
1.19
|
1.35
|
|||||||||||||||||||||||||||||||||||||||||||||||||||||||||||||||||||||||||||||||||||||||||||||||||||||||||||
Linear
density percentage of deviation (%)
|
0.6
|
0
|
-2.4
|
-1.8
|
-1.5
|
|||||||||||||||||||||||||||||||||||||||||||||||||||||||||||||||||||||||||||||||||||||||||||||||||||||||||||
Percentage
of length deviation (%)
|
-3.1
|
1.4
|
-2.3
|
-3.6
|
-0.3
|
|||||||||||||||||||||||||||||||||||||||||||||||||||||||||||||||||||||||||||||||||||||||||||||||||||||||||||
Over-length
staple fiber (%)
|
0.4
|
1
|
0
|
0
|
0
|
|||||||||||||||||||||||||||||||||||||||||||||||||||||||||||||||||||||||||||||||||||||||||||||||||||||||||||
Over-cut
fiber (mg/100g)
|
3.2
|
10.1
|
3.5
|
0
|
1.1
|
|||||||||||||||||||||||||||||||||||||||||||||||||||||||||||||||||||||||||||||||||||||||||||||||||||||||||||
Oil
content (%)
|
0.2
|
0.26
|
0.28
|
0.3
|
0.3
|
|||||||||||||||||||||||||||||||||||||||||||||||||||||||||||||||||||||||||||||||||||||||||||||||||||||||||||
Residual
sulfur (mg/100g)
|
12.2
|
18.4
|
9.5
|
11.8
|
10.5
|
|||||||||||||||||||||||||||||||||||||||||||||||||||||||||||||||||||||||||||||||||||||||||||||||||||||||||||
Whiteness
(%)
|
68.8
|
59.9
|
66.3
|
61.8
|
66.5
|
|||||||||||||||||||||||||||||||||||||||||||||||||||||||||||||||||||||||||||||||||||||||||||||||||||||||||||
Coefficient
of dry tenacity variation (CV)(%)
|
16.72
|
8.66
|
12.11
|
10
|
12.6
|
|||||||||||||||||||||||||||||||||||||||||||||||||||||||||||||||||||||||||||||||||||||||||||||||||||||||||||
Defect
(mg/100g)
|
3.4
|
3.7
|
3.6
|
0.6
|
2.7
|
|||||||||||||||||||||||||||||||||||||||||||||||||||||||||||||||||||||||||||||||||||||||||||||||||||||||||||
Oil-stained
fiber (mg/100g)
|
0
|
0
|
0
|
0
|
0
|
|||||||||||||||||||||||||||||||||||||||||||||||||||||||||||||||||||||||||||||||||||||||||||||||||||||||||||
Moisture
regain (%)
|
10.82
|
12.96
|
11.4
|
10.37
|
10.29
|
|||||||||||||||||||||||||||||||||||||||||||||||||||||||||||||||||||||||||||||||||||||||||||||||||||||||||||
Rate
|
GRADE
A
|
GRADE
A
|
GRADE
A
|
GRADE
A
|
GRADE
A
|
100%
Bamboo Ringspun Yarn Technical Data
|
|||||||
NE
|
16NE
|
21NE
|
24NE
|
30NE
|
32NE
|
40NE
|
50NE
|
NM
|
27NM
|
35.5NM
|
40.6NM
|
50.7NM
|
54NM
|
67.6NM
|
84NM
|
CV%
|
2
|
2
|
2.2
|
2.3
|
2.3
|
2.8
|
2.4
|
TWIST
|
523.1
|
583.7
|
781.7
|
712.8
|
724.8
|
815.7
|
930
|
TPI
|
13.08
|
16.51
|
19.54
|
17.82
|
18.12
|
20.39
|
23.25
|
CV%
|
2.6
|
3.2
|
2.81
|
3.79
|
3.38
|
2.46
|
3.8
|
STRENGTH(CN)
|
550.7
|
439.2
|
350
|
290.3
|
286.7
|
209.4
|
158
|
RKM
|
15.6
|
15.7
|
14
|
14.8
|
14.4
|
13.6
|
12.6
|
CV%
RKM
|
9
|
8.1
|
8.2
|
8.3
|
8.3
|
9.5
|
11.9
|
ELONGGATION(%)
|
12.5
|
11.9
|
11.4
|
11.4
|
11.1
|
10.3
|
9.7
|
CV%
ELONGGATION
|
13.2
|
12.1
|
10.3
|
10.1
|
9.4
|
9.5
|
13
|
IMPERFECTIONS
|
|||||||
THICK/1000M
|
5
|
7
|
8
|
10
|
10
|
35
|
40
|
THIN/1000M
|
4
|
1
|
1
|
1
|
1
|
4
|
14
|
NEPS/1000M
|
9
|
10
|
15
|
23
|
25
|
39
|
51
|
HAIRINESS%
|
4
|
3.98
|
4.13
|
5.2
|
4.3
|
3
|
4
|
U%
|
11.2
|
10.3
|
13.2
|
12.4
|
12.3
|
13.5
|
14.8
|
70%
Bamboo/30%cotton Ringspun Yarn Technical Data
|
|||
NE
|
21NE
|
32NE
|
40NE
|
NM
|
35.5NM
|
54NM
|
67.6NM
|
CV%
|
2
|
2.2
|
2.7
|
TWIST
|
580
|
725
|
816
|
TPI
|
16.4
|
18.12
|
20.4
|
CV%
|
3.15
|
3.35
|
3.35
|
RKM
|
13.6
|
12.3
|
11.8
|
CV%
RKM
|
8.3
|
8.5
|
9.5
|
ELONGGATION(%)
|
11.9
|
11.1
|
10.3
|
CV%
ELONGGATION
|
12
|
9
|
9
|
IMPERFECTIONS
|
|||
THICK/1000M
|
4
|
15
|
40
|
THIN/1000M
|
0
|
1
|
6
|
NEPS/1000M
|
10
|
29
|
47
|
HAIRINESS%
|
4
|
4.2
|
4.3
|
U%
|
10.4
|
12.3
|
13.9
|
Bamboo rayon filament
Anti bacterial test
|
item
|
test result
|
test result
|
75D/30F
|
120D/42F
|
||
Dtex
|
|||
Average
|
82.8
|
134.9
|
|
Deviation
|
-0.6
|
1.2
|
|
CV%
|
1.66
|
1.47
|
|
Dry tensile strength
(CN/dtex)
|
2
|
1.97
|
|
Dry elongation at
break (%)
|
12.8
|
12.8
|
|
Dry enlongaton CV%
|
8.68
|
8.39
|
|
Color evenness
|
3.5
|
3.5
|
|
F deviation
|
0
|
0
|
|
Sizing rate%
|
1.76
|
1.49
|
Physical Parameters Compared With Other Fibers
Testing Item
|
Measure
|
Cotton 100%
|
Bamboo100%
|
comparison
|
Testing method
|
||
Antibacterial
|
Sterilization
|
Log
|
4.4
|
1.3
|
3.4 Times Up
|
JAFET Method
|
|
Activity
|
Reduction
|
7.1
|
1.3
|
5.5 Times Up
|
|||
Electrostatic Propensity
|
Volt
|
(cotton)190
|
(cotton)15
|
12 Times Up
|
B Method
|
||
(wool)680
|
(wool)290
|
||||||
Water Absorption
|
%
|
74.2
|
115.7
|
60%Up
|
Tumble Jar Dynamic Test
|
||
Drying Rate
|
g/202.5cm2
|
27.32
|
32.58
|
20%Up
|
B Method
|
||
Breaking Strength
|
%
|
50
|
65
|
30%Up
|
Gas Detection Tube M.
|
||
Bursting Strength
|
N
|
(warp)827.1
|
(warp)833.4
|
15%
|
C.R.E, Grab Method
|
||
(weft)490.8
|
(weft)559.8
|
||||||
Abrasion Resistance
|
kgs/cm2
|
7.6
|
8.0
|
--
|
Diaphragm Method
|
||
Colorfastness To Light
|
Times
|
15000
|
Above20,000
|
30%Up
|
Martindale Method
|
||
Colorfastness To Washing
|
Grade
|
4-5
|
4-5
|
--
|
A-1 Method
|
||
Colorfastness To Rubbing
|
Grade
|
4-5
|
4-5
|
--
|
A-1 Method
|
||
Colorfastness To Perspiration
|
Grade
|
4
|
4
|
--
|
A-1 Method
|
top specification
|
3D×88mm
|
Average length
|
68.7mm
|
Standard weight
|
21
|
Moisture regain %
|
10.7
|
Average weight (m/g)
|
20.8
|
Weight unevenness %
|
0.97
|
Coefficient of
dispersion
|
20.1
|
Staple under 30mm
|
0.84
|
Ranges(+ -)
|
+0.4 -0.4
|
Mean-square
deviation
|
17.7
|
Nub/g
|
0.25
|
Physical parameters of Bamboo Top
No comments:
Post a Comment