Employer of Choice
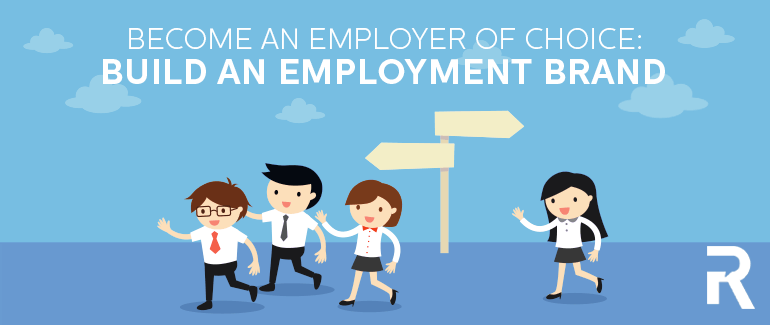
12 Characteristics of an Employer of Choice
An employer of choice strives to pay employees compensation that may include a salary and benefits that are equal to or above market rates. Most employers of choice offer employees a comprehensive employee benefits package, as they can afford to add benefits for employees, including health insurance, paid time off, paid holidays, and paid vacation.
Employers can consider themselves an employer of choice without these compensation offerings, but they must substitute a powerful mission or vision in their place. An example might be a non-profit agency with a mission to cure cancer in children.
These are examples of the additional factors that make an employer an employer of choice.
- Job Security: Employees are reasonably certain that their employer is financially sound. Freedom from concern about losing their jobs, employees are able to concentrate on their goals and core functions without worry.
- Empowerment and Authority: Employees are empowered to make decisions about and take responsibility for how they do their jobs. Employees are given a strategic framework (company mission, vision, values, goals, feedback) by their department, but they control their choices and how they perform their core functions and make progress on their goals.
- Respect: Employees may not always be right and their ideas may not set company direction and choices, but with an employer of choice, employees feel that they are fundamentally respected by their bosses and coworkers.
- Opportunity for Growth: At an employer of choice, employees feel as if they are encouraged to continue to develop their skills and careers. These employers offer performance development planning, career paths, and internal and external training opportunities. Job assignments help employees expand their skills.
- Access to Information: Employers of choice share information with employees that range from the company financial progress and results to the success framework referenced above. Employees feel as if they are members of the in-crowd because they know what is happening.
- Commitment: Employers of choice are committed to their employees and to their customers. This is reflected in everything from Human Resources policies to business strategies. This commitment plays out in retention and engagement strategies and perks that can range from free lunches and beverages to monthly employee and family events. Lunch with the president, inclusion in candidate interviews, and a place on an employee selection committee cement employee commitment and involvement. Running a boot camp for customers or a conference or training event at the company location highlight employer commitment and most of the other strategies on this recommended list.
- Involvement: At an employer of choice, employees feel as if they have the opportunity to be involved. They can make suggestions, think up new products or service innovations, serve on employee committees to plan events and work processes, and attend appropriate meetings and have input on work processes that affect their jobs.
- Positive Relationships With Coworkers: Gallup research finds that engaged employees are likely to have a best friend at work. On a larger scale, at an employer of choice, because the cultural fit is considered in recruitment, coworkers like and enjoy working with each other. A bad boss is dealt with by the organization before he or she can negatively impact employees and the work culture. Remember that for employee retention, employees leave bosses more than they leave anything else present in their workplace.
- Work-Life Balance: Increasingly demanded by employees, work-life balance initiatives such as flexible scheduling choices, allow employees to work undistracted by the family and life events and needs occurring outside of the workplace. These initiatives minimize employee stress and help them accomplish life's challenges while working.
- Performance Culture: An employer of choice finds ways to tie the performance and the interests of employees with those of the employer. Two of the ways that employers accomplish this are through their variable compensation system that ties rewards to performance and a job plan process that provides regular guidance and feedback.
- Fairness: Perceptions of unfair treatment or a workplace that favors certain individuals over others for unknown, undefined reasons, is an anathema to an employer of choice. Employers need to fairly develop and apply policies, treat employees with the same regard and consideration, and make the workplace guidelines clear and enforceable across the board.
- Recognition: Employers of choice provide feedback to employees about their performance, growth prospects, accomplishments, and areas needing improvement regularly. One of the most powerful forms of feedback is employee recognition. For an employer of choice, recognition is regular, targeted to real successes, and used to reinforce positive, desired behavior.
These are not all of the characteristics of an employer of choice, but if you've implemented a significant number of these factors in your company, you are well on your way to becoming an employer that attracts and retains superior employees.
Your reputation will proceed you and employees will seek you out as a desirable place to work. That's the first goal of any effective recruitment strategy. Be the employer that superior employees choose.
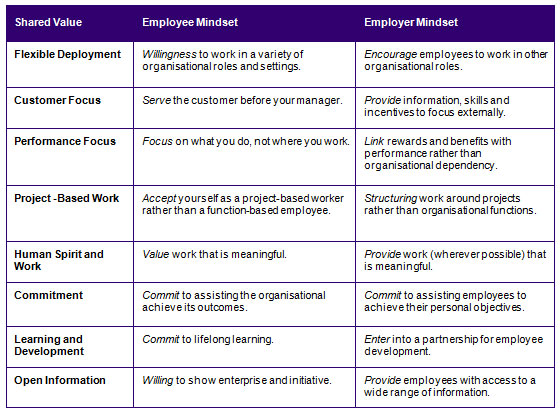
A recent Gallup study found that only 47 percent of American workers are completely satisfied with their jobs. A Market Tools study found that 21 percent of employees had applied to another job in the past six months. Clearly, many employees are ready to look elsewhere for the next step in their careers.
How do you make them look at you? More importantly, how do you make your current employees stay with you?
Or, in short, how can your company become an employer of choice?
Becoming an employer of choice means that applicants are eager to work for you, that people envy your employees, that you receive unsolicited resumes, and that your most talented workers stay with the company throughout their careers.
It’s the holy grail for every employers. So do you achieve it?
There’s no single answer to that question. In fact, coming up with the answer may require answers to more questions. Here are a few you should tackle:
- “Employer of choice” to whom? Determine who are the people you want to run your business. Shark-like go-getters? Tech wizards? Ideallists who want to change the world? Employees of your competitors? Your workers don’t have to be people who live nearby or happened to see your job listing. Create a vision for your workforce and strive to bring it to life. The answer to the first question leads to the second:
- What do the people that you want, want? A recent survey of college seniors by the National Association of Colleges and Employers found that, when weighing a job offer, these workers look first for opportunities for personal growth, then job security, and then friendly co-workers. “High starting salary” didn’t make the top three. So if you’re offering recent grad lots of money up front but little chances of career advancement, you’ll need to change your priorities to be successful. There are plenty of workplace surveys out there, but you’ll get the best information from your employees, your candidates (even the ones who turned you down), and your applicants. Ask them what drew them to your organization. What set you apart? What’s still lacking? Accept the answers without judgment. You can’t improve unless you acknowledge you’re not perfect. Spoiler alert: Answers to the next question may require collaboration with your senior leadership.
- What are you prepared to do to attract your ideal employees — and keep them? This may require some changes within your structure or culture. You may have to increase perks, change policies, or even enhance your workplace with, say, a gym, or daycare center, or coffee bar. And that can’t happen without approval of your senior leadership, who may not see the need behind such transitions (and costs). You can tell them that more engaged employees will lead to higher retention, lower hiring costs, higher productivity, and eventually greater profits — all true.
Every company wants to have an employer brand that positions them as an employer of choice. Who wouldn’t want to have talent competing for you instead of the other way around?
So, in addition to the answers to the questions above, here is a short list of attributes of an employer of choice.